Quality parts and easy to assemble & use. Works well with 220 volts, have used this sheet metal & tube plasma cutter a handful of times, cuts sheet metal from ⅛-½ smooth as butter. I'll try tube cutting in the next days. So far I am ecstatic about my purchase.
Square & Round Tube CNC Plasma Cutting Machine for Sale
Square/Round tube CNC plasma cutting machine is a professional automatic CNC metal pipe cutter with rotary tube pro software for round pipes or square tubes made of iron, steel, brass, copper, alloy, and other metals.
- Brand - STYLECNC
- Model - STP1530R
- Supplity - 360 Units in Stock Available for Sale Every Month
- Standard - Meeting CE Standards in Terms of Quality & Safety
- Warranty - One-Year Limited Warranty for Entire Machine (Extended Warranties Available for Major Parts)
- 30-Day Money Back Guarantee for Your Purchase
- Global Logistics and International Shipping for You
- Free Lifetime Technical Support for End-Users & Dealers
- Online (PayPal, Trade Assurance) / Offline (T/T, Debit & Credit Cards)
The CNC plasma cutting machine is a professional computer-controlled cutter used for cutting round and square metal pipe automatically with rotary tube pro software, which can realize automatic CNC programming and nesting job for any complex metal pipe. The CNC plasma tube cutting machine can cut any type of pipe in one go. This rotary plasma tube cutter is popular in steel structure, shipbuilding, bridge and heavy machinery industries.
The CNC plasma tube cutter is suitable for cutting cylindrical branch tubes, and two or three layer saddle cutting of main tubes, which makes it ideal for professional cross tube cutting in large quantities. In addition, customized designs are available according to the different needs of metal fabricators.
Square & Round Tube CNC Plasma Cutting Machine Applications
A CNC plasma cutting machine designed for square and round tubes offers versatility across various materials and industries. With its ability to handle different metals and shapes, this machine supports a range of applications and industries.
Materials Suitable for CNC Plasma Cutting
This CNC plasma cutter can handle a range of metals, making it ideal for diverse tasks. It efficiently cuts iron, aluminum, galvanized and stainless steel, carbon, and mild steel, as well as titanium and copper, in both tube and sheet formats. Its ability to process these materials supports a variety of industries, from small-scale projects to larger, high-demand manufacturing.
Industries Benefiting from CNC Plasma Cutting
This machine is applied across many fields, including the production of case shells for mechanical and electrical products, signage, and decorative items. It’s widely used in sectors like blacksmithing, landscaping, automotive, shipbuilding, electrical accessories, and welding. Its precision cutting capacity offers efficient, high-quality results, making it valuable for businesses centered on both detailed craftsmanship and large-scale output.
Technical Parameters of Square & Round Tube CNC Plasma Cutter
Model | STP1530R |
Working Area (X*Y) | 1500X3000mm |
Max Cutting Speed | 8000mm/min |
X, Y Transmissions | Hiwin Square Rail, Rack Drive |
Accuracy | 0.02mm |
Motor | Servo |
Plasma Cutter | Hypertherm |
Plasma Power | 45A - 200A |
Software | Fastcam |
Working Form | Untouched arc striking |
Control System | Beijing STARFIRE |
Power | 8.5KW |
Support Input | G-Code, HPGL, CAD, PLT |
Weight | 1800Kgs |
Dimension | 5200X2200X1970mm |
Input Voltage | 3-Phase 380V |
Power Frequency | 50Hz |
Files Transfer | USB interface |
Round & Square Tube CNC Plasma Cutting Machine Features
1. The CNC plasma rotary tube cutter is equipped with a professional control system for a variety of types of cuts, including tees, miters, saddles, centerline offsets, multiple intersections, elbow supports, gusset slots; Round, rectangular, saw cut, overlapping pipe holes, re-pads with axial offsets and baseline or work point offsets, and other types of intersecting cuts.
2. Precise casting parts and strict manufacture and test procedures ensure high accuracy, reliability, and durability.
3. Integrated with specialized programming and computing modules for complicated large steel structure construction, it can generate CNC codes from AutoCAD drawings to save operators and engineers time. These modules are compatible with IGES, DXF, SAT, and STL files.
4. Automatic, servo-driven height sensing system compensates vertical position for the out-of-round pipe. In-feed and out-feed conveyors are available for loading and unloading.
5. Professional CNC Controller for Plasma Tube Cutting Machine
6. Four Claws Rotary Device for Round & Square Tube Plasma Cutter
7. Plasma Cutting Torch
8. Plasma Cutting Torch with Drilling Head
9. Hypertherm PowerMax 85 Plasma Power Supply
10. Identification Plate for STP1530R
Round & Square Tube CNC Plasma Cutting Table Projects
Advantages of Using a CNC Plasma Cutter for Tube Cutting
A CNC plasma cutter used for tube cutting is valuable in the manufacturing area to do the job both quickly and accurately for a wide range of applications. This is why such a tool is ideal for the cutting of tubes in various materials and shapes for these reasons.
Precision Cuts
CNC plasma cutters use high-speed, controlled plasma jets to make accurate cuts. This precision is essential for tubes where alignment and size consistency impact the final structure. With exact cuts, manufacturers can rely on a more stable and high-quality final product.
Variability in Materials
CNC plasma cutters work well with various metals, starting from stainless steel to the highly resisting Titanium. They are suitable for square, round, and even uniquely shaped tubes. This adaptability allows the businesses to carry a variation in projects due to the existence of only one machine type, which results in being varied during fabrication.
Efficiency and Speed
These tube cutters, when combined with a CNC plasma cutter, can speed up fabrication processes by cutting metals fast and efficiently. With this kind of capability, the time consumed by bigger orders will be lessened hence improving productivity while at the same time minimizing costs of labor. Businesses can, therefore, deliver orders to customers more quickly while increasing satisfaction.
Cost-Effectiveness
Even though the upfront investment can be a lot higher, CNC plasma cutters avoid material waste by using very accurate cuts. They also reduce labor costs through automation, therefore saving money on long-term operational expenses. This efficiency ensures a very high return on investment, mainly in high-volume production.
Square vs. Round Tube Cutting: Unique Challenges and Solutions
Square and round tube cutting present distinct challenges, and understanding these differences helps operators achieve quality results. Below are common challenges with solutions for both types of cuts:
Challenges in Square Tube Cutting
Square tubes have flat surfaces that can cause drag or misalignment if not handled carefully. This geometry requires precise settings to avoid cutting errors. The solution lies in calibration and ensuring that the machine is properly aligned with each cut to maintain the tube’s shape.
Challenges in Round Tube Cutting
Round tubes, on the other hand, can slip or roll on the cutting bed, affecting cut precision. Ensuring the tube remains stable during cutting is key. Specialized rotary attachments are often used to keep the tube in place, allowing the machine to create consistent cuts as it rotates the tube.
Solutions for Consistent Results
Both square and round tube cutting benefit from high-quality fixtures to secure the material in place. With CNC plasma cutters, programming adjustments can help in positioning and calibrating the machine for each cut. Operators should regularly test settings for optimal cutting precision.
Considerations for Material Thickness
Both square and round tube cutting can be affected by material thickness. Thicker materials need stronger plasma arcs, which require careful calibration to avoid excessive wear on the cutter. Regularly checking machine settings helps maintain cut quality across different tube types and thicknesses.
Maintenance and Care for Square & Round Tube CNC Plasma Cutters
Proper maintenance of a CNC plasma cutter is essential for extending its lifespan and ensuring consistent performance. Here are essential care tips to keep your machine in peak condition:
1. Keep the Cutting Bed Clean: Clean the cutting bed after each use to prevent debris buildup. Metal fragments or slag left on the surface can cause misalignment and reduce cut quality. A regular cleaning routine also minimizes wear on the machine components.
2. Check and Replace Consumables: Regularly inspect consumables like nozzles, electrodes, and shields, as worn parts impact cut precision. Replace them as needed to maintain a smooth plasma arc. Tracking consumable wear can prevent sudden machine issues and improve consistency.
3. Cooling Systems: Plasma cutters do generate heat and, as such, require monitoring of the cooling systems. The coolant levels should be checked and the hoses inspected for leaks. Proper cooling prevents overheating and prolongs the lives of parts.
4. Peer Review: Grease all mobile points, for example, rails or bearings. Lack of lubrication may lead to friction, wearing out, and eventual breakdown. Regular lubrication helps reduce friction and offers smoother operations.
5. Electrical Connections: Check electrical connections, which should be secure and free from corrosion. Bad connections might bring about voltage fluctuations or even a power cutoff in time when the machine is supposed to be cutting. Good, stable electrical connections will go a long way in assuring good overall machine life and reliable operations.
Package of CNC Plasma Tube Cutter Machine
Professional CNC Plasma Cutting Machine for Round Metal Tube
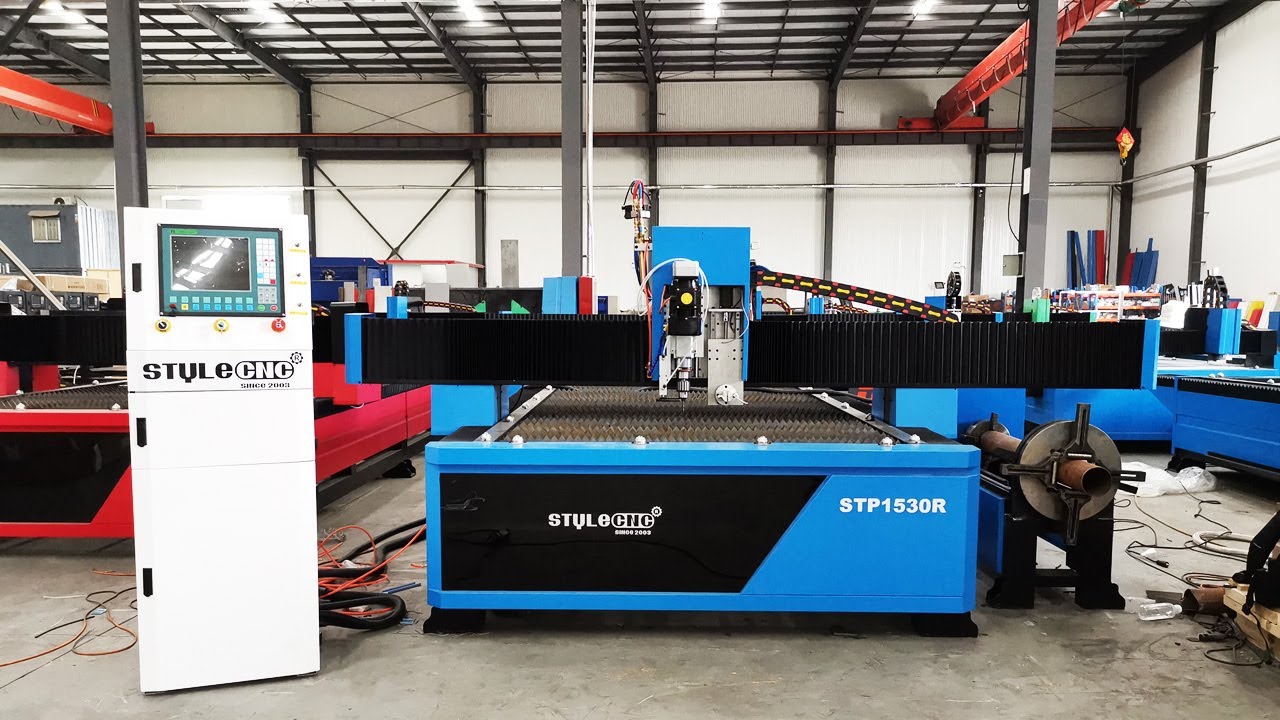
Randall Cunningham
Fang Yi
I was hesitant to buy this plasma table due to its price and abilities, but finally I decided to give it a try. It's so easy to use with CNC automation. I wanted to cut everything in my repair shop, and tried to cut through a few steel plates, as well as round tubing and square tubing. All worked smoothly with fast speed. Great cutter for what I paid for.