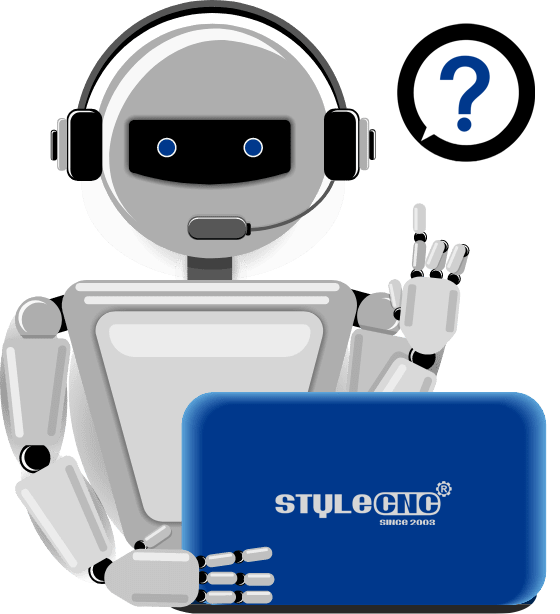
Concept
NC (Numerical Control)
NC is a technology that uses digital signals to automatically control objects (such as the motion of the machine tool and its working process), referred to as numerical control.
NC Technology
NC technology refers to the automatic control technology that uses numbers, letters and symbols to program a certain working process.
NC System
NC system refers to the organic integrated system of software and hardware modules that realize the functions of NC technology. It is the carrier of NC technology.
CNC System (Computer Numerical Control System)
CNC (Computer Numerical Control) system refers to the numerical control system with computer as the core.
CNC Machines
CNC machine refers to a machine tool that uses Computerized Numerical Control technology to control the machining process, or a machine tool equipped with a Computerized Numerical Control system.
NC Definition
Numerical Control is the full form of NC for machine tools. Numerical Control (NC) enables an operator to communicate with machine tools through numbers and symbols.
CNC Definition
CNC is the short name of Computer Numerical Control, which is an automatic technology of controlling machine tools to complete automated machining with CAD/CAM software in modern manufacturing process. New machine tools with CNC have enabled industry to consistently produce parts to accuracies undreamed of only a few years ago. The same part can be reproduced to the same degree of accuracy any number of times if the program has been properly prepared and the computer properly programmed. The operating G-code commands which control the machine tool are executed automatically with high speed, accuracy, efficiency, and repeatability.
CNC machining is a computerized manufacturing process, the machine is connected to a computer, the computer will tell it where to move. First, the operator should do the toolpath creation, the operator uses a software program to draw the shapes and create the tool path that the machine will follow.
The ever-increasing use in industry has created a need for personnel who are knowledgeable about and capable of preparing the programs which guide the machine tools to produce parts to the required shape and accuracy. With this in mind, the authors have prepared this textbook to take the mystery out of CNC - to put it into a logical sequence and express it in simple language that everyone can understand. The preparation of a program is explained in a logical step-by-step procedure, with practical examples to guide the user.
Component
CNC technology consists of three parts: bed frame, system and peripheral technology.
The frame kit is mainly composed of basic parts such as bed, column, guide rail, working table and other supporting parts such as tool holder and tool magazine.
The numerical control system is composed of input/output equipment, computer numerical control device, Programmable Logic Control (PLC), spindle servo drive device, feed servo drive device and measuring device. Among them, the device is the core of the numerical control system.
Peripheral technology mainly includes tool technology (tool system), programming technology, and management technology.
Glossary
CNC: Computer Numerical Control.
G-Code: A universal numerical control (NC) machine tool language that specifies axis points to which the machine will move.
CAD: Computer Aided Design.
CAM: Computer Aided Manufacturing.
Grid: The minimum movement, or feed of the spindle. The spindle automatically moves to next grid position when button is toggled in continuous or step mode.
PLT (HPGL): Standard language for printing vector-based line drawings, supported by CAD files.
Toolpath: User-defined, coded route which the cutter follows to machine the workpiece. A “pocket” toolpath cuts the surface of the workpiece; a “profile” or “contour” toolpath cuts completely through to separate the workpiece shape.
Step Down: Distance in Z-axis that the cutting tool plunges into the material.
Step Over: Maximum distance in X or Y axis that cutting tool will engage with uncut material.
Stepper Motor: A DC motor that moves in discrete steps by receiving signals, or “pulses” in a particular sequence, thus resulting in very precise positioning and speed control.
Spindle Speed: Rotational speed of cutting tool (RPM).
Conventional Cut: Cutter rotates against direction of feed. Results in minimal chatter but can lead to tearout in certain woods.
Subtractive Method: The bit removes material to create shapes. (Opposite of additive method.)
Feed Rate: Speed at which the cutting tool moves through the workpiece.
Home Position (Machine Zero): Machine-designated zero point determined by physical limit switches. (It does not identify actual work origin when processing a workpiece.)
Climb Cut: Cutter rotates with direction of feed. Climb cutting prevents tearout, but can lead to chatter marks with a straight-fluted bit; a spiral-fluted bit will reduce chatter.
Work Origin (Work Zero): The user-designated zero point for the workpiece, from which the head will perform all it's cutting. X, Y and Z axes are set to zero.
LCD: Liquid Crystal Display (used on the controller).
U Disk: External data storage device that is inserted into a USB interface.
Features
High Accuracy
CNC machines are highly integrated mechatronic products, which are composed of precision machinery and automatic control systems. They have high positioning accuracy and repeat positioning accuracy. The transmission system and the structure have high rigidity and stability to reduce errors. Therefore, Computerized Numerical Control machine has higher machining accuracy, especially the consistency of parts manufacturing in the same batch, and the product quality is stable, the pass rate is high, which is incomparable with ordinary machine tools.
High Efficiency
CNC machines can use a larger amount of cutting, which effectively saves processing time. They also have automatic speed change, automatic tool change and other automatic operation functions, which greatly shorten the auxiliary time, and once a stable processing process is formed, there is no need to perform inter-process inspection and measurement. Therefore, the productivity of Computerized Numerical Control machining is 3-4 times higher than that of ordinary machine tools, or even more.
High Adaptability
CNC machines perform automatic processing according to the program of the processed parts. When the machining object changes, as long as the program is changed, there is no need to use special process equipment such as masters and templates. This is helpful to shorten the production preparation cycle and promote product replacement.
High Machinability
Some mechanical parts formed by complex curves and curved surfaces are difficult to process or even impossible to complete with conventional techniques and manual operations, and can be easily realized by CNC machines using multi-coordinate axes linkage.
High Economic Value
CNC machining centers mostly use process concentration, and one machine is multi-purpose. In the case of one clamping, most parts of the parts can be processed. They can replace several ordinary machine tools. This can not only reduce clamping errors, save auxiliary time between transportation, measurement, and clamping between processes, but also reduce the types of machine tools, save space, and bring higher economic benefits.
Pros & Cons
Pros
Safety
The operator of the CNC machine is safely separated from all sharp parts by a special protective structure. He can still see what's going on at the machine through the glass, but he doesn't need to go anywhere near the mill or spindle. The operator also does not have to touch the coolant. Depending on the material, some liquids may be harmful to human skin.
Save Labor Costs
Today, conventional machine tools require constant attention. This means that each worker can only work on one machine. When the CNC era came, things changed dramatically. Most parts take at least half an hour to process each time they are installed. But computer numerical controlled machines do it by cutting the parts themselves. No need to touch anything. The tool moves automatically, and the operator simply checks for errors in the program or settings. Having said that, CNC operators find they have a lot of free time. This time can be used for other machines. So one operator, many machine tools. This means you can save manpower.
Minimum Setting Error
Traditional machine tools rely on the operator's proficiency with measuring tools, and good workers can ensure parts are assembled with high precision. Many CNC systems use specialized coordinate measurement probes. It is usually mounted on the spindle as a tool and the fixed part is touched with a probe to determine its position. Then, determine the zero point of the coordinate system to minimize the setup error.
Excellent Machine Condition Monitoring
The operator must identify machining faults and cutting tools, and his decisions may not be optimal. Modern CNC machining centers are packed with different sensors. You can monitor torque, temperature, tool life and other factors while machining your workpiece. Based on this information, you can refine the process in real time. For example, you see that the temperature is too high. Higher temperatures mean tool wear, poor metal properties, etc. You can reduce the feed or increase the coolant pressure to fix this. Despite what many say, machining is the most widespread manufacturing method today. Every industry uses machining to some degree.
Stable Accuracy
What's more stable than a proven computer program? The movement of the instrument is always the same because its accuracy depends only on the accuracy of the stepper motors.
Fewer Test Runs
Traditional machining inevitably has some test parts. The worker has to get used to the technology, he will definitely miss something when doing the first part and testing the new technology. CNC systems have a way to avoid test runs. They employ a visualization system that allows the operator to actually see the inventory after all the tools have passed through.
Easy Machining Complex Surface
Manufacturing complex surfaces with high precision is nearly impossible with conventional machining. It requires a lot of physical labor. CAM systems can automatically form toolpaths for any surface. You don't have to put in any effort at all. This is one of the greatest advantages of modern CNC machining technology.
Higher Cutting Data
High-speed machining is only possible due to the closed cutting area. At this speed, the chip flies all over the place at high speed. There is a coolant spray after the chips, because when it comes to high-speed machining, the coolant is applied under high pressure. Manual operation is simply not possible when the speed reaches 10000 rpm or more. With high cutting speeds, it is important to keep the feed rate and chip width stable to prevent vibration. It can't be hard to do it manually.
Higher Flexibility
The traditional method is that milling machines for grooves or flats, lathes for cylinders and tapers, and drilling machines for holes. CNC machining can combine all of the above into one machine tool. Since tool trajectories can be programmed, you can replicate any motion on any machine. So we have milling centers that can make cylindrical parts and lathes that can mill grooves. All of this reduces the set-up of the part.
Cons
High technical requirements for operators and machine maintenance personnel;
Computer numerical control system is not easy to control, not as intuitive as ordinary machine tools;
The purchase cost of the machine tool is more expensive.
Applications
From the perspective of CNC technology and equipment applications in the world, its main application areas are as follows:
Manufacturing Industry
The machinery manufacturing industry is the earliest industry to apply Computerized Numerical Control technology, and it is responsible for providing advanced equipment for various industries of the national economy. The main applications are the development and manufacturing of five-axis vertical machining centers for modern military equipment, five-axis machining centers, large-scale five-axis gantry milling, flexible manufacturing lines for engines, gearboxes, and crankshafts in the automotive industry, and high-speed machining centers, as well as welding, assembly, painting robots, plate laser welding machines and laser cutting machines, high-speed five-coordinate machining centers for machining propellers, engines, generators and turbine blade parts in the aviation, marine and power generation industries, heavy duty turning and milling complex machining center.
Information Industry
In the information industry, from computer to network, mobile communication, telemetry, remote control and other equipment, it is necessary to adopt manufacturing equipment based on super-precision technology and nanotechnology, such as wire bonding machines for chip manufacturing, wafer lithography machines. The control of these equipment needs to use Computerized Numerical Control technology.
Medical Equipment Industry
In the medical industry, many modern medical diagnosis and treatment equipment have adopted numerical control technology, such as CT diagnostic instruments, whole body treatment machines and minimally invasive surgical robots based on visual guidance, orthodontics and dental restoration in stomatology are required.
Military Equipment
Many modern military equipment use servo motion control technology, such as automatic aiming control of artillery, tracking control of radar and automatic tracking control of missiles.
Other Industries
In the light industry, there are printing machinery, textile machinery, packaging machinery and woodworking machinery that use multi-axis servo control. In the building materials industry, there are computer numerical controlled waterjet cutting machines for stone machining, computer numerical controlled glass engraving machines for glass machining, computer numerical controlled sewing machine used for simmons processing and computer numerical controlled embroidery machine used for clothing processing. In the art industry, more and more crafts and artworks will be produced using high performance 5 axis CNC machines.
The application of numerical control technology not only brings revolutionary changes to the traditional manufacturing industry, making the manufacturing industry a symbol of industrialization, but also with the continuous development of numerical control technology and the expansion of application fields, it has played an increasingly important role in national economy and people's livelihood (e.g. IT and automobile) , light industry, medical treatment, because the digitization of equipment required in these industries has become a major trend in modern manufacturing.
Trends
High Speed / High Precision
High speed and precision are the eternal goals of machine tool development. With the rapid development of science and technology, the speed of replacement of electromechanical products is accelerated, and the requirements for the precision and surface quality of parts processing are also higher and higher. In order to meet the needs of this complex and changeable market, the current machine tools are developing in the direction of high-speed cutting, dry cutting and quasi-dry cutting, and the machining accuracy is constantly improving. In addition, the application of linear motors, electric spindles, ceramic ball bearings, high-speed ball screws and nuts, linear guide rails, and other functional components has also created conditions for the development of high-speed and precision machine tools. The computer numerical control machine tool adopts an electric spindle, which eliminates the links such as belts, pulleys, and gears, which greatly reduces the moment of inertia of the main drive, improves the dynamic response speed and working accuracy of the spindle, and completely solves the problem of vibration and noise when the spindle runs at high speed. The use of electric spindle structure can make the spindle speed reach more than 10000r/min. The linear motor has high drive speed, good acceleration and deceleration characteristics, and has excellent response characteristics and following accuracy. The use of linear motor as servo drive eliminates the intermediate transmission link of the ball screw, eliminates the transmission gap (including backlash), the motion inertia is small, the system rigidity is good, and it can be precisely positioned at high speed, thereby greatly improving the Servo accuracy. Due to its zero clearance in all directions and very small rolling friction, the linear rolling guide pair has small wear and negligible heat generation, and has very good thermal stability, which improves the positioning accuracy and repeatability of the whole process. Through the application of linear motor and linear rolling guide pair, the rapid moving speed of the machine can be increased from the original 10-20m/min to 60-80m/min, or even as high as 120m/min.
High Reliability
The reliability is a key indicator of the quality of computer numerical controlled machine tools. Whether the machine can exert its high performance, high precision and high efficiency, and obtain good benefits, the key depends on its reliability.
CNC Machine Design with CAD, Structural Design with Modularization
With the popularization of computer applications and the development of software technology, CAD technology has been widely developed. CAD can not only replace the tedious drawing work by manual work, but more importantly, it can carry out design scheme selection and static and dynamic characteristic analysis, calculation, prediction and optimization design of large-scale complete machine, and can carry out dynamic simulation of each working part of the whole equipment. On the basis of modularity, the three-dimensional geometric model and realistic color of the product can be seen in the design stage. The use of CAD can also greatly improve work efficiency and improve the one-time success rate of design, thereby shortening the trial production cycle, reducing design costs, and improving market competitiveness. The modular design of machine tool components can not only reduce repetitive labor, but also respond quickly to the market and shorten product development and design cycles.
Functional Compounding
The purpose of functional compounding is to further improve the production efficiency of the machine tool and minimize the non-machining auxiliary time. Through the compounding of functions, the use range of the machine tool can be expanded, the efficiency can be improved, and the multi-purpose and multi-function of one machine can be realized, that is, a CNC machine can realize both the turning function and the milling process. Grinding is also possible on machine tools. Computer numerical controlled turning and milling compound center will work with X, Z axes, C and Y axes at the same time. Through the C axis and the Y axis, plane milling and machining of offset holes and grooves can be realized. The machine is also equipped with a powerful tool rest and a sub-spindle. The sub-spindle adopts a built-in electric spindle structure, and the speed synchronization of the main and sub-spindles can be directly realized through the numerical control system. The machine tool workpiece can complete all processing in one clamping, which greatly improves the efficiency.
Intelligent, Networked, Flexible and Integrated
The CNC equipment in the 21st century will be a system with certain intelligence. The content of intelligence includes all aspects of the numerical control system: in order to pursue the intelligence in machining efficiency and machining quality, such as the adaptive control of the machining process, the process parameters are automatically generated; in order to improve the driving performance and use the intelligence in connection, Such as feedforward control, self-adaptive operation of motor parameters, automatic identification of load, automatic model selection, self-tuning, etc.; simplified programming, simplified operation intelligence, such as intelligent automatic programming, intelligent interface, intelligent diagnosis, intelligent monitoring and other aspects to facilitate the diagnosis and maintenance of the system. Networked numerical control equipment is a hot spot in the development of machine tools in recent years. The networking of CNC equipment will greatly meet the needs of production lines, manufacturing systems, and manufacturing enterprises for information integration, and it is also the basic unit for realizing new manufacturing models, such as agile manufacturing, virtual enterprises, and global manufacturing. The development trend of computer numerical controlled machines to flexible automation systems is: from point (stand-alone, machining center and composite machining center), line (FMC, FMS, FTL, FML) to surface (independent manufacturing island in workshop, FA), body (CIMS, distributed network integrated manufacturing system), on the other hand to focus on the direction of application and economy. Flexible automation technology is the main means for the manufacturing industry to adapt to dynamic market demands and to rapidly update products. Its focus is to improve the reliability and practicality of the system as the premise, with the goal of easy networking and integration, and pay attention to strengthening the development and improvement of unit technology. CNC stand-alone machines are developing in the direction of high precision, high speed and high flexibility. CNC machines and their constituent flexible manufacturing systems can be easily connected with CAD, CAM, CAPP and MTS, and develop towards information integration. The network system develops in the direction of openness, integration and intelligence.
STYLECNC is a self-owned brand of Jinan Style Machinery Co., Ltd. As a leading enterprise of intelligent manufacturing in China, we are constantly innovating and developing over 20 years, our efforts bring us stable customers from home and abroad, you can find STYLECNC products in over 180 countries from Europe, Africa, Mid east, America, Oceania and Southeast Asia, which drive us to be a worldwide CNC machine brand.
Jinan Style Machinery Co., Ltd. was founded in 2003, which is an enterprise with core technology and independent intellectual property rights, we are committed to the development and manufacture of CNC machines.
You can check as following to determine if STYLECNC is legit:
1. STYLECNC has legal business qualifications.
2. The contact information is visible.
3. STYLECNC has a business entity.
4. STYLECNC has a real location.
5. There are no online complaints about STYLECNC.
6. STYLECNC can provide approved business contracts.
7. STYLECNC has official business email.
8. STYLECNC has proper website registration, the official website is professional.
Laser-cutting acrylic is one of the latest additions to our technological advancement that enables an efficient fabrication process of acrylic sheets and offers unparalleled precision in engraving, carving, or shaping them. This high-powered tech opened a world of creative possibilities.
But, today we are not going to praise the laser cutting of acrylic with what it can do. Rather, in this post we will be exploring the safety considerations of this tech and find out if it is toxic or not. We will also deliver safety measures and guidelines to follow before taking your project to the field.
The importance of understanding the safety considerations and following them is crucial. Let’s find out whether and how effectively the laser cutting acrylic revolutionized manufacturing industries.
A Brief Overview of Laser Cutting Acrylic
Laser cutting acrylic uses high voltage concentrated laser beam to cut through the materials. It offers a wide range of applications. The laser beam precisely cuts through or engraves acrylic sheets. This is way better than traditional milling or sawing methods. Efficient productivity and ease of usability make laser-cutting acrylic sheets popular these days.
Utilizing the intense heat generated by the laser cuts and shapes the material with smooth finishing and clean edges. Laser cutter offers superior accuracy to the task.
Understanding Safety Considerations and Importance
This newly added tech is undoubtedly more beneficial than any traditional milling and cutting methods. However, laser cutting acrylic also leads to potential hazards and safety risks. Today, our primary concern is the safety considerations and importance of those laser cutting acrylics.
Safety considerations in laser cutting acrylic are crucial. Lack of safety measurement will cause several hazards, such as health hazards, inhalation difficulties, eye injuries, skin irritation sensitization, and so on.
To avoid any unwanted experience follow these rules and make sure safety features are enabled.
✔ Proper ventilation is very important at work. The process creates fumes and gasses. Direct inhalation exposure can cause severe health issues within days.
✔ A complete PPE set can save you from many long-term physical diseases due to working with the laser beam. A proper PPE setup features organic vapor cartridges and safety goggles to protect against inhalation of fumes and potential eye damage from laser radiation.
✔ Make sure regular maintenance to maximize efficiency and performance. This will also save you from any potential machine malfunction or accidents.
✔ Emphasize the training and education of the operators. With proper knowledge and expertise, an operator can save the machinery along with him from any potential disabilities.
✔ Practice and ensure regulatory compliance provided by legal authorities.
Now, safety considerations bear great importance and significance due to probable hazardous incidents. Therefore, STYLECNC recommends prioritizing the safety steps to attain physical and financial safety on top.
Chemicals Released During Laser Cutting
Laser cutting uses high-voltage electric power to generate high-temperature heat. The concentrated laser beam then vaporizes the material with a predetermined path by a CNC software system and shapes the item accordingly.
In this whole machining process, a few chemicals and bi-products are produced as waste. Here, we have given a brief look at the chemicals produced during laser cutting acrylic.
Methyl Methacrylate (MMA)
The properties of Methyl Methacrylate and the health effects due to this chemical exposure are given below.
• Methyl methacrylate is a colorless liquid with a sweet odor
• Commonly used in acrylic plastics, adhesives, coatings, and resins production
• Skin contact can cause irritation, redness, and dermatitis for skin-sensitive personnel
• Even a short-time exposure to concentrated MMA can cause respiratory tract
• MMA is also considered a potential carcinogen
Now the exposure limits and regulations in laser cutting acrylic are necessary to learn and follow.
OSHA and ACGIH established exposure limits and guidelines for MMA to protect workers from diverse health effects. The OSHA permissible exposure limit (PEL) for MMA is 100 parts per million (ppm). The ACGIH threshold limit value (TLV) for MMA is 50 ppm as an 8-hour TWA.
Formaldehyde
Knowing the health hazards and carcinogenicity of Formaldehyde will certainly help keep you on a safe track. It is a colorless gas with a distinct odor. Health hazards prone to take cause are likely,
• Inhalation of the gas can irritate the eyes. Besides, the nose, throat, and respiratory tract are common hazards of the exposure
• Repeated and long exposure to Formaldehyde is responsible for severe health diseases like asthma, and bronchitis, as well as allergic reaction
• The International Agency for Research on Cancer (IARC) and the National Toxicology Program (NTP) classified Formaldehyde as a known human carcinogen
To reduce hazards due to this chemical substance regulatory guidelines are established by OSHA and ACGIH.
The OSHA permissible exposure limit (PEL) for Formaldehyde is 0.75 parts per million (ppm) and the ACGIH threshold limit value (TLV) for Formaldehyde is 0.3 ppm as an 8-hour TWA. OSHA has established a short-term exposure limit (STEL) of 2 ppm as well for formaldehyde. This is crucial to know about the regulatory guidelines for all operators.
Hydrogen Cyanide (HCN)
This is a highly toxic element found during the production of materials with coating and additives. Specific coated acrylic products can produce HCN. During acrylic cutting high temperature of the laser can produce a decomposition product like cyanide.
The health risks of this chemical element are high. So, safety measures for acrylic laser cutting are a must.
Inhalation of hydrogen cyanide vapor can lead to symptoms such as headache, dizziness, nausea, vomiting, difficulty breathing, and in severe cases, loss of consciousness and death. To minimize the chances of any health issues ensure the following steps,
Proper ventilation system, and personal protective equipment (PPE), monitor performance, and train the workers with adequate knowledge.
Health Risks Associated with Acrylic Fumes
Neglecting the importance of safety considerations and not following them can cause severe physical harm. Working for a long time to exposure to HCN can cause death.
Respiratory effects
• Irritation and discomfort: Exposure to fumes and gas and inhalation of irritant substances such as Methyl Methacrylate and formaldehyde, can cause acute respiratory irritation.
• Long-term health implications: Chronic exposure to acrylic fumes causes respiratory diseases such as bronchitis, asthma, and chronic obstructive pulmonary disease (COPD).
Skin and Eye Irritation
• Contact dermatitis: Contact with acrylic fumes can lead to contact dermatitis. Symptoms of contact dermatitis may include redness, itching, swelling, and blistering of the skin.
• Eye irritation and damage: Exposure to laser radiation consistently can cause eye irritation and damage.
Safety Precautions for Laser Cutting Acrylic
Safety precautions are essential to reduce the chance of accidents while laser cutting acrylics. Follow the safety measures and ensure a safe work environment. Some important safety measures are,
✔ Make sure proper ventilation in the cutting area to remove fumes and gases.
✔ Install fume extraction equipment or local exhaust ventilation.
✔ Provide appropriate PPE to the operators and workers.
✔ Make sure the workers wear respirators with organic vapor cartridges to avoid direct inhalation of fumes and gases.
✔ Use safety goggles and protective gloves on working.
✔ Ensure routine inspection and maintenance check-ups of the laser acrylic cutting machine.
✔ Train operators and workers.
✔ Follow the instruction manual given by the manufacturer.
Regulatory Compliance and Standards
Relevant regulations and guidelines for regulatory compliance are made to ensure the safety of the health and workers of cutting acrylic. These standards are established and approved by the Occupational Safety and Health Administration (OSHA), the National Institute for Occupational Safety and Health (NIOSH), and the International Organization for Standardization (ISO).
The OSHA regulations are:
⇲ Hazard Communication Standard (HCS).
⇲ Respiratory Protection Standard.
⇲ Personal Protective Equipment (PPE).
⇲ Ventilation Standard.
NIOSH also features a couple of standard guidelines for workers engaged with laser cutting acrylic for exposure to both Methyl Methacrylate and Formaldehyde.
There are a few ISO standards as well to follow.
Best Practices for Safe Laser Cutting Operations
To ensure a safer laser cutting operation operators and owners must follow all the safety considerations and regulations we talked about. A few tactics to make sure workers are healthy and safe are given below.
Training and education for operators
Provide comprehensive training to your workers for laser cutting acrylic including setup, shut down, and operation. Make sure they are trained for emergency response.
Regular maintenance of equipment
Take routine inspections of machines and parameters. Check parts and components like laser sources, optics, cooling systems, and safety interlocks, to identify and address any signs of wear, damage, or malfunction.
Monitoring and testing for air quality
Do take regular ventilation checks and install essential equipment to make sure the environment and air quality are breathable.
You can find CNC router machines (CNC wood routers, stone carving machines, metal CNC machines, 3D CNC routers, 3 axis CNC routers, 4 axis CNC routers, and 5 axis CNC routers), CNC laser machines (laser marking machines, laser engraving machines, laser cutting machines, laser cleaning machines, and laser welding machines), CNC milling machines, CNC plasma cutting machines, CNC machining centers, CNC wood turning lathe machines, digital cutting machines, automatic edge banding machines, CNC spare parts, and other CNC machines from STYLECNC in over 180 countries from Europe, Africa, Mid east, America, Oceania and Southeast Asia, we can contact our customer to arrange a visit for you.
Laser engraving of metals has become increasingly accessible even to makers on a budget. While the diode lasers are at a relative disadvantage compared to the fiber lasers when it comes to power, they are quite capable of impressive engravings in their own right.
From choosing the right diode laser to understanding the possible challenges one may face, this article will show how to undertake best practices in helping you overcome them. By the end of this article, you will have an idea of what you need to get confident with laser engraving in metal, making sharp detailed designs that stand the test of time. Now, let's get into it and start unlocking the potential of diode lasers for your metal engraving projects.
Can You Engrave Metal with a Diode Laser?
Engraving metal with a diode laser is possible, but it requires knowledge of the laser's capabilities and limitations. Unlike fiber lasers designed specifically for metal, diode lasers are less powerful and may struggle with hard metals or deep engravings. However, with the right setup and materials, they can achieve detailed markings and surface-level engravings on softer metals like aluminum or coated surfaces. Using techniques like pre-treating the metal with marking sprays or paints can significantly enhance engraving results.
Diode lasers are flexible tools usually preferred due to their affordable and adaptable nature. In cases where it has worked well with non-metal material, advanced laser technology now allows users to try engraving with metal effectively. With patience and the proper settings, diode lasers will be able to provide appropriate budget-friendly solutions for hobbyists and small-scale projects that require metal engraving.
How to Laser Engrave Metal with Diode Laser?
While the idea of engraving metal with a diode laser may seem challenging, it is, in fact, pretty doable considering proper setup and approach. Diode lasers, not as powerful as industrial fiber lasers, provide an affordable alternative and versatile solution for making small projects. Here is a step-by-step guide in achieving precise and professional results in engraving metal using a diode laser.
Choose the Right Metal and Preparation
Not all metals are suitable for diode laser engraving. Softer metals like aluminum or coated metals yield the best results. To enhance engraving quality, apply a laser marking spray or paste to the surface. These coatings react with the laser, creating a durable and high-contrast mark. Ensure the metal surface is clean and free of dust or grease before applying the spray.
Optimize Laser Settings
Proper laser settings are crucial for effective engraving. Adjust the power, speed, and focus of the diode laser to match the material. Lower speeds with higher power settings work best for engraving metal. Perform test engravings on scrap pieces to fine-tune the settings before starting your final project.
Focus the Laser Precisely
Accurate focusing ensures better energy concentration on the metal surface. Adjust the laser head to the optimal height as specified in your machine's manual. Many diode lasers come with adjustable focus lenses or automatic focusing features to simplify this process.
Use Multiple Passes for Deeper Marks
Diode lasers typically require multiple passes to create noticeable engravings on metal. Instead of increasing power excessively, use several passes at moderate power to avoid damaging the laser or the material. Monitor progress between passes to achieve the desired depth.
Work in a Ventilated Area
Engraving metal can produce fumes, especially when using marking sprays. Ensure your workspace is well-ventilated, or use an air extraction system. Safety goggles and gloves are essential to protect yourself during the process.
Post-Engraving Finishing
After engraving, the metal surface should be cleaned of any residues or remnants of spray. Use a soft cloth or mild cleaning solution to enhance the appearance of the engraving. This will make the engravings more prominent and pleasing to the sight.
How to Choose the Right Diode Laser for Metal Engraving?
Choosing the right diode laser is paramount to a high-quality metal engraving. Different models with different features mean one should make informed decisions in terms of the efficiency, precision, and durability of the projects. Here is a guide on how to choose a perfect diode laser for metal engraving.
Consider Laser Power and Wavelength
The power of the diode laser determines the ability of engraving on metal effectively. The minimum or higher power output that a laser should have to engrave on metal should be at least 5 watts. The wavelength is important, too; lasers at about 450nm are normally used for diode laser engraving and yield quite reliable performance on metal surfaces, especially with marking sprays.
Evaluate Compatibility with Metal Engraving
Not every diode laser is made for metal engravings. Ensure that the model of your laser supports engraving on metal surfaces, or at least that it can be used with laser marking sprays or coatings that enhance performance. Look up user reviews and specifications from manufacturers to ensure compatibility.
Focus Adjustment and Precision
A diode laser with an adjustable focus mechanism is essential for engraving metal accurately. Precise focusing ensures optimal energy delivery to the surface, resulting in cleaner and more detailed engravings. Look for features like manual or automatic focus adjustment for added convenience.
Software and User Interface
The software accompanying the diode laser should be user-friendly and compatible with your design needs. Look for machines that support popular formats like SVG, DXF, or PNG, and check if the software includes options for adjusting engraving speed, power, and resolution.
Build Quality and Safety Features
Durability is vital when choosing a diode laser. Opt for models with robust builds and safety features such as protective shields, emergency stop buttons, and reliable cooling systems. These features ensure both longevity and safe operation.
Materials Compatible with Diode Laser Metal Engraving
Diode lasers can honestly be called all-rounders, but in many respects, the possibility of metal engraving again shows itself to be dependent upon material properties and the application of laser marking sprays or coatings. A look at which metals can be worked with, and what you can expect from their engravings.
1. Stainless Steel: Diode lasers can engrave stainless steel effectively when used with a marking spray. This creates high-contrast marks that are durable and ideal for industrial or artistic purposes.
2. Aluminum: Anodized aluminum responds well to diode lasers, producing clear and sharp engravings without additional coatings. For raw aluminum, a marking spray enhances the engraving results.
3. Brass: Brass can be engraved using a diode laser with the help of marking sprays. The process highlights fine details, making it suitable for decorative or branding applications.
4. Copper: The high reflectivity of copper makes it hard to engrave, but a high-powered diode laser can work well along with marking sprays or coatings.
5. Titanium: Diode lasers engrave on titanium, yielding highly detailed designs or text, and are often used in custom jewelry or medical device labeling.
6. Coated Metals: Lacquered or powder-coated metals are engraved so easily with diode lasers because the varnish gets burned away and the base material comes to view.
7. Soft Metals: Diode lasers can do engraving on metals like zinc and tin, though results may vary depending on thickness and reflectivity.
Common Challenges in Diode Laser Metal Engraving and How to Overcome Them
Engraving metal with a diode laser is an exciting process, but it comes with challenges that can impact the quality of your work. By understanding and addressing these issues, you can achieve more precise and professional results.
Insufficient Laser Power
Diode lasers are similar to UV lasers, typically have lower power compared to fiber or CO₂ lasers, which can limit their ability to engrave metals directly. This often results in shallow or faint engravings. To address this, you can use marking sprays or pastes to enhance the engraving effect. Alternatively, choosing a higher-wattage diode laser can improve results for tougher metals.
Poor Contrast in Engraving
Achieving visible engravings on metal can be tricky, especially with alloys or finishes that do not interact well with the laser. Improper power or speed settings often lead to uneven or dull engravings. Pre-treating the metal surface with marking agents or using coated metals can significantly enhance contrast. Regular testing on scrap pieces is also crucial to fine-tune your settings.
Overheating the Material
Heat generated during engraving can warp thinner metals or discolor surfaces. This is especially problematic for delicate or highly detailed designs. Using lower power settings and slower speeds helps control heat buildup. Additionally, ensuring proper ventilation or cooling during engraving can prevent unwanted heat effects.
Reflective Surfaces Interfering with the Laser
Highly reflective metals, like polished aluminum or brass, can scatter the laser beam, leading to inconsistent results. Applying a non-reflective coating to the surface before engraving helps improve absorption and reduces beam scattering. Adjusting the laser angle can also minimize reflection issues.
Inconsistent Results Across Materials
Different metals react uniquely to diode lasers, resulting in varying engraving quality. Experimenting with individual settings for each material and maintaining a log of optimal parameters ensures consistent outcomes. Regular practice and testing are key to mastering diverse materials.
Maintenance Tips for Diode Lasers Used in Metal Engraving
Proper maintenance will go a long way in ensuring long-term performance and quality metal engravings with your diode laser. Regular maintenance will prevent costly repairs, improve results, and prolong the life of your laser system.
• Cleaning the Lens and Mirrors: There is a lot of dust and debris that might accumulate at the lens and mirrors, affecting the focus and power of the laser. Wipe gently with a soft, lint-free cloth with appropriate cleaning solution for all these parts for good performance.
• Check the Cooling System: There is an coolant system that prevents the overheating of a laser. Check the level of coolant and change the fluid for its proper working.
• Grease Moving Parts: With a certain time span, the applied moving parts such as rails and motors are likely to get worn, causing the risk of jamming or misalignment. Put the recommended grease on these parts for their smooth working without mechanical issues.
• Inspect Wiring and Connections: The main cause of this can be loose or damaged wires that may result in performance inconsistencies or even safety hazards. Periodically check the wiring and connections for wear and ensure everything is securely connected.
• Monitor Laser Power and Calibration: Laser power may degrade over time with use, leading to less effective engraving. Regularly check the power output and recalibrate the laser to maintain consistent engraving quality.
• Software Update: Older versions of software contribute to inefficiency and sometimes incompatibility. Always keep your diode laser software updated to take advantage of fresh features and bug fixes.
• Clean the Work Surface: A clean working surface ensures that any possibility of interference from the remains is avoided. Remove all metallic shavings, dust, or residue to have the engraving area fresh and ready for work with accuracy.
Due to the complexity of the machine tool, the manufacturing cycle is different, and the shipping time is also different for different locations.
1. For 3 axis CNC router and milling machine with standard specification, usually 7-15 days.
2. For 4 axis CNC router and mill with standard specification, usually 20-30 days.
3. For high end 5 axis CNC machine, OEM or Non-standard models, usually 60 days.
4. For laser engraver, laser cutter, laser marking machine, laser cleaning machine, laser welding machine usually 5-10 days.
5. For high power laser cutting machine, usually 30-50 days.
6. For CNC wood turning lathe machine, usually 7-10 days.
7. For CNC plasma cutter & table kits, usually 7-10 days.
There is a lot to consider before you buy a CNC machine. You have to decide what type of CNC machine you want, which features it needs to have, and how you're going to pay for it. The listed ways below are the payment methods we accept.
Telegraphic Transfer
TT (Telegraphic Transfer) is the method of payment by electronic transfer of funds from one bank account to another.
Telegraphic transfers are also known as telex transfers, abbreviated TT. They can also refer to other types of transfers. The payment abbreviation, as is often the case, is utilized to speed discussions in professional circumstances. Telegraphic transfer is a fast nature of the transaction. Generally, the telegraphic transfer is complete within two to four business days, depending on the origin and destination of the transfer, as well as any currency exchange requirements.
e-Checking
Credit Card
Credit card payments with Visa or Mastercard are supported.
All the CNC machines can be shipped worldwide by sea, by air or by international express logistics via DHL, FEDEX, UPS. You are welcome to get a free quotation by filling up the form with name, email, detailed address, product and requirements, we will shortly contact you with the full information including the most suitable delivery method (fast, secure, discreet) and freight.
A CNC machine firstly should be packaged well in a free-fumigation wooden crate. Usually, we deliver the CNC machine by ship, sometimes, as customer's requirements, we can also deliver by air or by train. When the CNC machine arrived at your sea port or destination, you can pick up with the bill of lading we offered. We can also arrange the cargo agent to send to your door.
If you're shopping for a new or used CNC machine in today's marketplace. This list explores the easy-to-flow steps a buyer would take to purchase a CNC machine. Let's begin.
Step 1. Consult: we will recommend the most suitable CNC machines to you after being informed by your requirements.
Step 2. Quotation: We will supply you with our detail quotation according to our consulted machines with the best quality and price.
Step 3. Process Evaluation: Both sides carefully evaluate and discuss all the details of the order to exclude any misunderstanding.
Step 4. Placing Order: If you have no doubts, we will send you the PI (Proforma Invoice), and then we will sign a sales contract.
Step 5. Production: We will arrange the production as soon as receiving your signed sales contract and deposit. The latest news about production will be updated and informed to the buyer during the production.
Step 6. Inspection: The whole production procedure will be under regular inspection and strict quality control. The complete machine will be tested to make sure they can work very well before out of factory.
Step 7. Delivery: We will arrange the delivery as the terms in the contract after the confirmation by the buyer.
Step 8. Custom Clearance: We will supply and deliver all the necessary shipping documents to the buyer and ensure a smooth customs clearance.
Step 9. Support and Service: We will offer professional technical support and service by Phone, Email, Skype, WhatsApp around the clock.
We typically build CNC machines to standard designs, however in some cases we can provide custom services as listed below.
1. Table sizes can be larger or smaller depending on your specific CNC machining needs.
2. Your logo can be put on the machine whether you are an end user or a dealer.
3. The appearance and color of the machine are optional according to your personal preference.
4. Individual machine specifications can be designed in a customer-oriented manner.
Note: If you can't find your answer in the FAQs above, please ask a new question in the form below.
Ask Your Question
Asking questions is essential in CNC machining for fostering understanding and encouraging exploration, allowing individuals to gain deeper insights and challenge assumptions, ultimately facilitating learning and innovation.