Professional CNC Wood Carving Machine for Furniture Making
Large format professional CNC wood carving machine with automatic tool changer and 4th rotary axis is used for making furniture, cabinets, tables, chairs, doors, windows.
- Brand - STYLECNC
- Model - STM1625D-R1
- Table Size - 1600mm x 2500mm
- Supplity - 360 Units in Stock Available for Sale Every Month
- Standard - Meeting CE Standards in Terms of Quality & Safety
- Warranty - One-Year Limited Warranty for Entire Machine (Extended Warranties Available for Major Parts)
- 30-Day Money Back Guarantee for Your Purchase
- Global Logistics and International Shipping for You
- Free Lifetime Technical Support for End-Users & Dealers
- Online (PayPal, Trade Assurance) / Offline (T/T, Debit & Credit Cards)
What Are CNC Wood Carving Machines?
CNC wood carving machines are advanced devices made to precisely carve wood and create intricate shapes. These devices are ideal for making furniture because they allow manufacturers to swiftly and effectively produce fine pieces with detailed carvings. In contrast to traditional hand-carving techniques, CNC machines operate based on computer-controlled commands, which guarantees precision and minimizes human error.
In furniture making, CNC wood carving machines handle tasks like engraving patterns, cutting joints, and shaping decorative elements. They are capable of working on a variety of wood types, making them suitable for everything from cabinets and chairs to ornate headboards. With their ability to replicate designs consistently, they help save time and labor. This makes them a popular choice for both small workshops and large-scale manufacturers.
Overall, these machines provide a balance of precision, speed, and creativity, making them an essential tool for modern furniture production. They also open up new design possibilities that might be difficult to achieve with traditional methods.
Advantages and Features of CNC Wood Carving Machine
1. The CNC wood router machine with disc ATC system is an economical processing center with a linear type knife library. The main accessories of the CNC machine are from the world's top brands.
2. The CNC woodworking machine comes with an Italy 9.0KW HSD air-cooled spindle, and the drive system adopts a Japan servo motor.
3. Vacuum adsorption table, high adsorption power can adsorb different sizes of material.
4. Intelligent processing cross-border protection is to prevent the mechanical impact phenomenon caused by the excessive design layout then processing format.
5. The Syntec control system can do multi-level 3D processing automatically.
6. The wood CNC machine can do three-dimensional processing with fast, smooth carving/cutting, and it can be realized offline operation.
7. Dust cover for the Z axis, Y guide, and rack on the same side.
8. High speed and efficiency and carved smooth clear.
9. The woodworking CNC machine adopts a 4th axis rotary device, which can process cylinder materials, such as wood legs, and chair legs. The rotary diameter and length can be optional.
Technical Parameters of CNC Wood Carving Machine with Disc ATC System
Model | STM1625D-R1 |
Working Area | 1600x2500x200mm |
Traveling Positioning Accuracy | ±0.01/300mm |
Repositioning Accuracy | ±0.01mm |
Table Surface | Vacuum table |
Frame | Welded Steel Tube Structure |
X, Z Structure | Square Rails and TBI Ball Screw, |
Y Structure | Hiwin Rail Linear Bearings and Ball Screw |
Max Rapid Travel Rate | 60000mm/min |
Max Working Speed | 40000mm/min |
Spindle Power | 9kw HQD ATC Spindle |
Spindle Speed | 24000RPM |
Drive Motor | 1500W Servo System |
Working Voltage | AC380V or AC220V |
Command Language | G Code |
Operating System | Syntec |
Computer Interface | USB |
Flash Memory | 128M(U Disk) |
Collet | ER32 |
X, Y Resolution | <0.01mm |
Software Compatibility | Type3/ArtCAM Software |
Optional Parts | Chinese 9KW HQD ATC Spindle |
Chinese Servo Motor | |
LNC Control System | |
T-Slot Table |
Details of CNC Wood Carving Machine with Disc ATC System
D300, L2000mm Rotary Axis.
Electronic Box.
12PCS Disc ATC Tools Storage.
Italy HSD 9KW ATC Spindle.
Taiwan Syntec Control System.
Disc ATC CNC Wood Carving Machine Package.
Applicable Industries and Materials of CNC Wood Carving Machine
Furniture Decoration Industry | • A large area of flat panel engraving. • Panel furniture carving. • Wood art murals. • Wood cabinet door carving, wooden doors, cabinets, plates, office and wood furniture, table,chair, doors and windows. |
Wood Products Processing | • Sewing machine table. • Electrical counter table. • Sports equipments. |
Musical Instrument Industry | • Instrument 3D surface engraving. • Shape cutting, plastic chemical components, PCB, inner body of the car, bowling tracks, stairs, ABS, PP, PE and other carbon mixed compounds. |
Artwork | • Photo frame. • Jewelry box, PVC, MDF, acrylic, artificial stone, organic glass, plastic, and soft metals such as copper, aluminum plate engraving and milling process. |
Electronic Industry | • Circuit board. • Insulation material. • LED display screen. |
Projects of CNC Wood Carving Machine with Disc ATC System
STM1530D-R1 Carrousel Type Tool Storage ATC CNC Router for Option
Benefits of Using CNC Wood Carving Machines for Furniture Production
The process of creating furniture has been totally transformed by CNC wood carving machines, which offer precision, speed, and versatility. These tools offer several advantages, regardless of how big your manufacturing business is or how tiny your workshop is. They allow businesses to cut costs and increase design options while producing high-quality furniture efficiently and staying competitive in the market.
1. Increased Precision and Consistency: CNC machines can reproduce the same design with high precision, eliminating the inconsistencies that often occur with manual work. Every piece of furniture maintains the same quality, improving customer satisfaction.
2. Faster Production Time: Automation allows CNC machines to complete tasks more quickly than hand-carving. This speeds up the production process, helping businesses meet tight deadlines and increasing overall efficiency.
3. Reduced Labor Costs: With CNC machines handling complex carvings, businesses require fewer skilled workers. This reduces labor costs while maintaining or improving product quality.
4. Versatile Design Capabilities: CNC wood carving machines can execute intricate patterns and designs that are difficult to achieve by hand. This allows furniture makers to offer more creative and customized pieces to their clients.
5. Less Material Waste: These machines follow precise cutting paths, minimizing material wastage. This makes production more cost-effective and environmentally friendly.
6. Improved Scalability: Whether producing a single piece or hundreds, CNC machines can adapt easily. This flexibility helps businesses scale their operations as demand grows without compromising quality.
How to Choose the Right CNC Wood Carving Machine for Your Business
Making the right CNC machine choice can have a significant impact on your company. An efficient machine lowers expenses and facilitates the seamless achievement of production targets. Before you invest, keep these important things in mind.
Determine Your Production Needs
Think about the size and complexity of the furniture you plan to create. If you regularly work on larger pieces like tables or cabinets, opt for a machine with a bigger work area. Machines with multi-axis capabilities are also helpful for handling detailed projects.
Assess the Machine's Features
Look for essential features such as spindle power, cutting speed, and tool change options. Higher spindle power ensures smoother cuts on hardwood types, while faster speeds increase productivity. Machines with automatic tool changers save time by switching tools mid-process.
Evaluate Compatibility with Design Software
Ensure the CNC router works with software like ArtCAM, VCarve, or Fusion 360. Compatibility makes it easy to integrate custom designs and update them when needed. Using familiar software can also reduce the learning curve for your team.
Check the Machine's Durability and Build Quality
Choose machines built with strong materials like steel or cast iron to avoid frequent breakdowns. Well-constructed machines withstand heavy usage, reducing wear and tear over time. A durable build also minimizes vibrations, leading to more accurate cuts.
Consider Your Budget
Set a realistic budget based on your production goals and available resources. While premium machines offer advanced features, even a basic model can serve smaller operations effectively. Be sure to account for additional costs like installation and training.
Support and Warranty
Make sure the machine comes with a warranty covering key components and technical support. Access to training and repair services helps keep your operations running smoothly. Some manufacturers also provide online troubleshooting tools for faster problem resolution.
Maintenance Tips for Long-Lasting Performance of CNC Wood Carving Machines
Regular maintenance is essential for keeping your CNC wood carving machine in excellent shape. Here are some straightforward tips to help you maintain smooth performance and avoid expensive repairs. A properly maintained machine operates more efficiently and has a longer lifespan, which can save you both time and money over time.
• Keep the Machine Clean
Dust, wood shavings, and debris can gather on the surface and moving parts of the machine. Regular cleaning prevents blockages that can affect movement and precision. A clean machine ensures better performance and reduces the chance of mechanical issues.
• Lubricate Moving Components
Lubricate the machine's rails, bearings, and lead screws frequently to reduce friction. Smooth movements are essential for precise cuts and consistent performance. Neglecting lubrication can lead to premature wear and costly repairs.
• Inspect the Spindle and Cooling System
Regularly check the spindle for any unusual noises, vibrations, or signs of overheating. Make sure the cooling system is functioning properly to prevent heat damage to components. A healthy spindle is key to accurate carving and cutting results.
• Tighten Electrical Connections
Loose wires or electrical connections can interrupt the machine's operation and cause malfunctions. Periodically inspect and secure all connections to avoid unexpected downtime. Proper electrical maintenance improves safety and machine reliability.
• Update Firmware and Software
Manufacturers release updates with new features, bug fixes, and performance enhancements. Keeping the software and firmware up to date ensures the machine operates efficiently. Regular updates also help avoid compatibility issues with design software.
• Monitor for Signs of Wear
Check key components such as belts, screws, and bearings for wear and tear. Replace damaged or worn parts promptly to maintain optimal performance. Early detection of wear prevents larger problems from developing.
By adhering to these maintenance guidelines, you can make sure that your CNC wood carving machine runs efficiently and delivers dependable results for many years. Consistent care not only reduces downtime but also maximizes your return on investment.
FAQs for Professional CNC Wood Carving Machine for Furniture Making
What Is a CNC Wood Carving Machine?
A CNC wood carving machine is a computer-controlled tool that carves designs into wood. It uses precise movements to create detailed shapes and patterns. This technology is widely used in furniture making for its accuracy and efficiency.
How Does a CNC Wood Carving Machine Work?
The machine operates using a computer program that guides the cutting tool. It moves along multiple axes to carve the wood as per the design. This allows for intricate and consistent results, saving time compared to manual carving.
What Materials Can Be Used with a CNC Wood Carving Machine?
CNC wood carving machines primarily work with various types of wood, including hardwoods and softwoods. They can also handle composite materials and certain plastics. However, using the right tools and settings for different materials is essential for optimal results.
What Are the Benefits of Using a CNC Wood Carving Machine for Furniture Making?
Using a CNC machine enhances precision and speed in furniture production. It reduces labor costs and minimizes human error. Additionally, it allows for complex designs that might be difficult to achieve by hand.
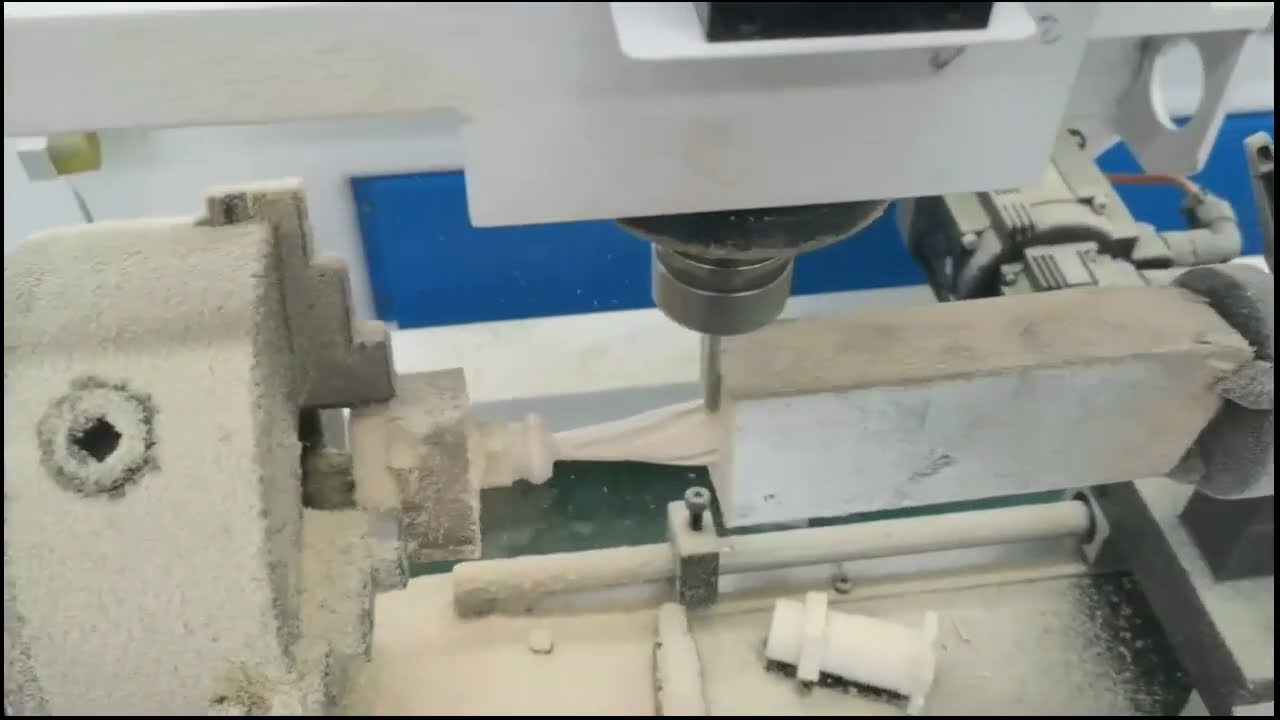
Valentina
Martin McElroy
James Cobb
Don't have to assemble, everything works well, and seems nice and tight. The included windows program works fine on Windows 7, I may switch to some other Mac or Raspberry Pi based program but this was an easy way to get started.
Adam Wisnia
Perfectly wrapped. Very easy to assemble. The wood carving machine works very well. This is the best one I've seen for this sort of CNC for a long time.