2025 Best 4 Axis CNC Foam Router Cutting Machine for Sale
4 axis CNC foam router cutting machine is used to mill & cut foam board, Styrofoam, EPS foams, XPS foams, and rigid polystyrene foams into various 2D/3D shapes, and now the CNC foam cutter for sale at affordable price.
- Brand - STYLECNC
- Model - STM1530
- Supplity - 360 Units in Stock Available for Sale Every Month
- Standard - Meeting CE Standards in Terms of Quality & Safety
- Warranty - One-Year Limited Warranty for Entire Machine (Extended Warranties Available for Major Parts)
- 30-Day Money Back Guarantee for Your Purchase
- Global Logistics and International Shipping for You
- Free Lifetime Technical Support for End-Users & Dealers
- Online (PayPal, Trade Assurance) / Offline (T/T, Debit & Credit Cards)
CNC foam cutter is a type of automatic computer numerical controlled router machine to cut rigid foam, soft foam, sponge, and plastic into squares, rectangles, and strips. The foam cutting machine is a computer controlled machine that can cut any 3D projects from the extruded and expanded EPS foam. Through the use of a computer-controlled step motor, the heating wire is cut in the X, Y and Z directions, which can make the foam material cut quickly and accurately. The operator can make any graphics with the CNC router software and start cutting with CNC control system, which has the advantages of high cutting efficiency, accurate cutting size, and high precision. The scope of application is suitable for machinery manufacturing, casting, automobiles, ships, industrial design, mold manufacturing and processing, advertising, architectural decoration and decoration, foam cutting plants, foam manufacturing plants, foam molding plants, school institutions, advertising production companies, packaging plants, exhibitions, Model factories, POP crafts processing and publicity display industries. CNC foam cutters are also known as CNC foam cutting machines, CNC foam board cutter, CNC foam router and CNC foam cutting kits.
4 Axis CNC Foam Router Cutting Machine Advantages
1. Specialized in making large non-metallic molds, especially automobile foam molds, ship molds, aviation train molds, food molds (such as cake molds), and other molds.
2. The built-in rotating axis is used to process any three-dimensional cylindrical materials for woodworking, advertising, and mold industries.
3. The spindle can rotate 180 degrees and can mill some arched workpieces.
4. The Z axis can be raised to 1000mm, which can perform large-scale three-dimensional curve milling.
4 Axis CNC Foam Cutting Machine Applications
Applicable Industries
1. Mold making industry: Large sculptures and foam molds.
2. Musical Instrument Industry: 3D musical instruments and silhouettes.
3. Non-Ferrous Metals: Aluminum, brass, copper, alloys, and other light non-ferrous metals.
Applied Materials
1. Timber and wood.
2. EPS as well as any type of foam.
3. Plastic and acrylic.
4. Aluminum, brass and copper.
4 Axis CNC Foam Router Machine Features
1. The machine bed is welded with thickened square tubes, and is treated with high temperature tempering and vibration aging treatment (VSR) to eliminate residual stress. It has good stability, is not easy to deform, and has the characteristics of good rigidity and strong bearing capacity.
2. The machine comes with Hiwin high-precision square guide rails, and the X and Y axes adopt gear rack transmission, which is fast, efficient and low cost. The Z axis adopts German-made ball screws with high precision and long life.
3. The machine adopts gantry movement and can freely process various materials.
4. The intelligent processing out-of-bounds protection function can prevent mechanical shock caused by improper design files.
5. The machine adopts imported ball bearings, widened linear guide rails, and self-lubricating sliders. During processing, the force in all directions is uniform to ensure accuracy and strength.
6. The machine features the functions of breakpoint continuation and power-off re-engraving.
7. The machine has the function of machining time prediction.
8. The machine works with a diversified control system, which can control the processing speed, idling speed and cutting speed respectively, greatly improving the processing quality.
4 Axis CNC Foam Router Cutting Machine Technical Parameters
Model | STM1530 |
X,Y Working Area | 1500×3000mm |
Z Working Area | 600mm |
Resolution | 0.5mm |
Repositioning Accuracy | 0.5mm |
Lathe Structure | Seamless welded steel structure, better than cast iron one |
X,Y Structure | Rack and pinion transmission, Hiwin square guide rail |
Z Structure | Germany-made rolling ball screw, Hiwin square guide rail |
Max. Idling Speed | 30m/min |
Spindle | 6kw spindle |
Spindle Rotate Speed | 0-24000r/min, variable speed |
Working Voltage | AC380V/50Hz |
Working Mode | Servo motor and diver |
Command | G code (HPGL,U00,mmg,plt) |
Operating System | Nc studio |
Diameter of cutter | φ3.175-φ12.7mm |
Cooling Mode | Water-cooling |
Work-holding | By clamp |
Net Weight | 3000KG |
Software | Type 3, ArtCam, Ucancam |
4 Axis CNC Foam Milling & Cutting Projects
4 Axis CNC Foam Milling & Cutting Machine Details
Maintenance Tips for Your 4-Axis CNC Foam Cutter
Proper maintenance is crucial for ensuring the longevity and efficiency of your 4-axis CNC foam cutter. Regular care not only reduces downtime but also maintains precision and performance over time. Follow these essential tips to keep your machine in top condition.
• Clean the Machine Regularly: Foam debris can accumulate on the work table and around the cutting head. Clean these areas after every session to prevent clogging or misalignment. Use a soft brush or vacuum to remove small particles safely.
• Lubrication of Moving Parts: Smear lubricants on the rails, ball screws, and other moving parts. This reduces friction, thus preventing damage that may cause inoperability of parts. Check the recommendations of the manufacturer to apply the right lubricant.
• Check and Fix Components: With time, fittings such as screws and belts are loosened by vibrations. Check these fittings once in a while and replace them when necessary. It ensures accuracy in operation.
• Check the Cutting Tool: Check the cutting tool for any indication of wear: a dull edge or even any small cracks. Replace or sharpen the tool to keep the cuts clean and precise. Using worn tools can cause the foam to tear or the machine to be strained.
• Keep an Eye on the Cooling System: If your machinery has a cooling system, then make sure it works effectively. Never allow blockages in the flow of coolant; in addition, the levels are to be controlled with recommendations. Proper cooling avoids overheating and prolongs machine life.
• Calibrate the Tests Frequently: Frequently check on the calibration tests so that the movements of the machine will be exact. For proper calibration, there will be no mistakes in cutting the foams, and the quality of every work will be just the same.
• Update Software and Firmware: The first important thing to be done is to update the software and firmware in such a way that the machine remains updated with freshly released features and enhancements. Of course, it will take care of bugs and improve the general performance.
STYLECNC SERVICE for 4 Axis CNC Foam Router Cutting Machine
Before Order
Technical support and suggestions before you order a foam CNC milling & cutting machine according to your work piece.
Guarantee
The guarantee period shall be 12 months counting from the date on which the foam CNC cutting machine arrives destination port. Except for the damage artificially, we are responsible for offering the fittings free of charge during the guarantee period, but you must send the damaged fittings to us by courier with your charge before we send back the alternative fittings to you. After the guarantee of the quality period, the parts required to repair or change, if any, shall be paid.
Installation and Debugging
Customers can get detailed operation manuals and instruction videos. We will make sure that customers can operate CNC foam milling cutting machines skillfully.
After-Sale Service
24-hour technical support by email or call.
Our technician will come to your workshop if the problems can not be fixed through Internet or phone communications.
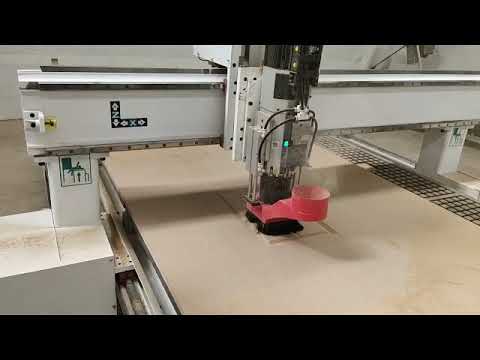