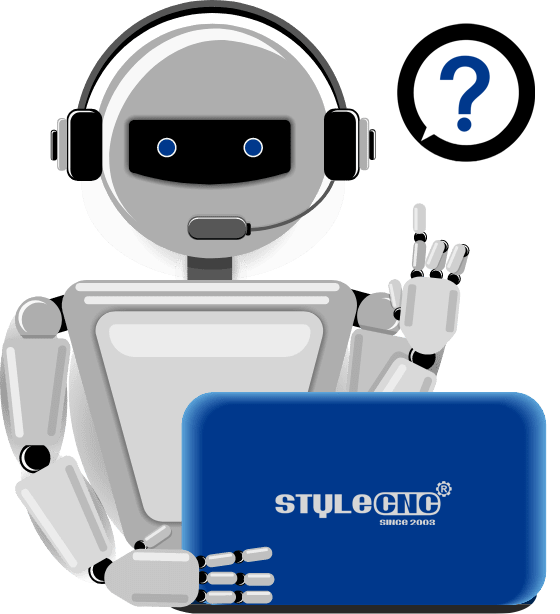
Industry applications such as metalworking, engraving, woodworking, and others now depend heavily on CNC (Computer Numerical Control) equipment. Their accuracy, productivity, and aptitude for managing intricate assignments are well-known attributes. A lot of attention has been paid to Chinese-made CNC machines throughout the years. Their affordability is one of the key causes of this. Still, a lot of prospective customers wonder: Are Chinese CNC machines any good?
This article will examine the features, dependability, performance, and quality of CNC machines made in China to provide an answer to that query. We'll also discuss how long they last, if they're appropriate for small enterprises, and offer advice on selecting a quality machine.
Quality of Chinese CNC Machines
Prices are sometimes the first thing that comes to mind when we think about Chinese items. There are questions regarding quality because Chinese CNC machines are far less expensive than equivalent models in Europe or America. Chinese manufacturers were once known for taking shortcuts. However, in recent years, many Chinese enterprises have improved their production standards, especially in fields like CNC technology.
• Better Technology: Many Chinese manufacturers now use advanced technology to produce CNC machines that meet international quality standards. This means machines are more precise, durable, and reliable.
• Improved Quality Control: Factories have adopted stricter quality control processes to ensure that their machines can compete globally. Today, you’ll find many Chinese CNC machines that comply with certifications like ISO9001, which guarantees certain levels of quality and performance.
• Global Collaboration: Some Chinese manufacturers partner with international companies to produce high-quality machines. This collaboration allows them to incorporate better designs and use higher-quality materials.
In general, the quality of Chinese CNC machines has improved significantly. Chinese CNC machines are used in many industries, such as metal fabrication, woodworking, and automotive since they produce high-quality outputs at an affordable price.
Are Chinese CNC Machines Any Good?
Let's now discuss the primary question "Are Chinese CNC machines any good?" The answer isn’t as easy as a "yes" or "no" because it relies on various things, such as the individual equipment, the manufacturer, and what you plan to use it for. Investing in Chinese CNC machines can be wise, particularly if you're searching for a cost-effective option. To guarantee that you receive a machine that satisfies your needs, you must select a reliable manufacturer. These are some important things to remember.
1. Affordability: Compared to machines from Europe or the United States, CNC machines made in China are far less expensive. Because of this, they are a desirable choice for small and medium-sized companies without the funding for luxury brands. Cheaper doesn't always result in worse quality. Excellent value for the money is offered by many CNC machines made in China.
2. Varied Quality: The quality of Chinese CNC machines can vary from one manufacturer to another. While some businesses may offer more affordable, less durable equipment, others may build high-quality machines that function well and survive for years. Doing your homework on a brand is crucial before making a purchase.
3. Customer Satisfaction: Many users report positive experiences with Chinese CNC machines, particularly in industries like woodworking and metalworking. They find the machines capable of handling their production needs efficiently.
4. Customization Options: Customizable features are available on several Chinese CNC manufacturers' machines. This lets customers select particular parts, apps, or features according to their needs. This flexibility can offer excellent value because it allows you to customize a machine to meet your particular needs without having to pay extra for things that aren't necessary.
5. Availability of Spare Parts: One advantage of buying Chinese CNC machines is the availability of spare parts. Many Chinese manufacturers provide easy access to replacement parts, which can be shipped quickly and at lower costs compared to parts for Western machines. This can reduce downtime and keep production running smoothly.
Performance and Reliability of Chinese CNC Machines
The performance and reliability of CNC machines are critical for any business, as they directly impact production efficiency. So how do Chinese CNC machines fare in terms of performance and reliability?
Performance
Chinese CNC machines are well-known for their high performance in general-purpose activities such as cutting, milling, and engraving. These machines can deal with a variety of materials, including wood, plastic, and metal. Many Chinese CNC machines can operate at fast speeds, allowing enterprises to produce more in less time.
Advanced models are appropriate for businesses that need exquisite detailing, like jewelry production and sign engraving, because they can handle complex designs and high-precision activities. In terms of performance, many Chinese CNC machines are comparable to models made in Europe and America, particularly when used in non-industrial environments.
Reliability
A crucial component of every CNC machine is reliability. When properly maintained, Chinese CNC machines can be quite dependable. Regular upkeep such as oiling, cleaning, and component inspections can help the equipment last longer. However, when purchasing from less popular manufacturers, some customers have occasionally reported having problems with warranty claims or customer assistance.
Chinese CNC machines are highly dependable when maintained regularly and work well in a variety of applications. Selecting a model that aligns with your manufacturing requirements is crucial.
Common Features of Chinese CNC Machines
Chinese CNC machines often come with a set of features that make them versatile and user-friendly. Here are some of the common features you’ll find,
• Affordable Pricing: The biggest selling point of CNC machines made in China is their affordability. These machines cost significantly less than models from other countries, making them accessible to businesses of all sizes.
• Wide Range of Models: Chinese CNC machines range from entry-level desktop units for beginners to industrial-grade machines for mass production, available in a variety of sizes and models. This range enables you to select a machine that meets your unique requirements.
• User-Friendly Interfaces: Easy-to-use control panels and intuitive software are standard on a lot of CNC machines made in China. This makes them usable even by novices who might not have much background in CNC technology.
• Multi-Functionality: Most Chinese CNC machines can handle multiple tasks, such as engraving, cutting, milling, and drilling. This versatility makes them suitable for various industries, including woodworking, metalworking, and plastic fabrication.
• Customization Options: You can adjust the machine to suit your production demands thanks to customization possibilities offered by certain Chinese manufacturers. Customization can improve the machine's functionality, whether it's through spindle upgrades or feature additions.
How to Choose a Good Chinese CNC Machine?
It might be difficult to select the best CNC machine, especially with so many alternatives available. The following guidelines will assist you in choosing a high-quality Chinese CNC machine. You can select a CNC machine that meets your company's requirements by using the procedures outlined here to help you make an informed choice.
1. Research the Manufacturer: Not every Chinese company manufactures similarly high-quality machinery. Seek out producers who have a solid track record, glowing testimonials, and dependable customer service. It can also be beneficial to look for international certifications such as ISO9001.
2. Know Your Requirements: Determine your needs for the machine before making a purchase. Will you be working with wood, metal, or plastic? Do you require extreme precision? Selecting the ideal machine for your organization can be made easier if you are aware of your needs.
3. Check for Warranties and Support: A good warranty can give you peace of mind in case something goes wrong. Also, make sure the manufacturer or supplier provides customer support, so you can get assistance if needed.
4. Read Reviews: User reviews can provide valuable insights into the performance and reliability of a machine. Look for reviews from businesses similar to yours to get a better idea of how well the machine will perform in your setting.
5. Evaluate Technical Specifications: Pay close attention to the technical specifications of the CNC machine. Look for details like the machine's speed, cutting accuracy, and the range of materials it can handle. Make sure the specifications align with your production needs.
Are Chinese CNC Machines Suitable for Small Businesses?
Cost is frequently a key consideration for small businesses when buying equipment. Chinese CNC machines are a popular option for small and medium-sized businesses (SMEs) because they are usually less expensive than their Western equivalents. Are they appropriate for such companies?
Chinese CNC machines are a wonderful solution for small companies for various reasons. First, they are affordable, so businesses on a tight budget can use them. Local businesses can compete in their markets by making cost-effective investments in CNC technology.
Scalable CNC machines are common in China. This suggests that companies can begin with a simple model and then update as they expand. Small businesses that intend to grow over time and require equipment that can adjust to their rising production needs will find this flexibility ideal.
The ease of use is another benefit. Chinese CNC machines are usually easy to operate thanks to their user-friendly interfaces. Small firms will benefit from this as it saves time and lessens the need for in-depth training. All things taken into account Chinese CNC machines offer a good mix of affordability and functionality, which makes them an excellent choice for small enterprises trying to streamline their processes.
Pros and Cons of Buying a Chinese CNC Machine
Like any product, Chinese CNC machines have advantages and disadvantages of their own. If you perform an in-depth study and consider your particular needs, you may make a better decision. Examine carefully the advantages and disadvantages of buying one.
Advantages of a Chinese CNC Machine
1. Affordable: Chinese CNC machines are much cheaper than those made in Western countries. This affordability makes them an attractive option for small businesses and hobbyists who may not have a large budget.
2. Versatile: A great deal of work may be done by many CNC machines made in China. They are capable of milling, engraving, and cutting a variety of materials, such as plastic, metal, and wood. This adaptability makes them suited for numerous applications.
3. Customizable: Some manufacturers allow for customization of their CNC machines. This means you can modify features or add components based on your specific needs. Customization can help you get the exact machine that fits your business requirements.
4. Wide Range of Models: China offers a wide range of CNC machines for sale. From compact desktop machines for amateurs to bigger industrial machines for heavy-duty manufacturing, there are types to suit every demand.
5. Rapid Production: Chinese manufacturers often have faster production times. This means you can get your machine sooner than from some other countries, allowing you to start your projects more quickly.
6. Availability of Spare Parts: Spare components are widely available from numerous Chinese manufacturers. This accessibility guarantees that you can quickly replace parts when necessary, cutting down on downtime and maintaining the efficiency of your operations.
Drawbacks of a Chinese CNC Machine
1. Varied Quality: The quality of Chinese CNC machines can differ significantly from one manufacturer to another. While some machines are high-quality, others may not meet your expectations. It is crucial to research and choose a reputable brand.
2. Customer Support: Some Chinese manufacturers may provide limited customer support, especially for international buyers. This can make it challenging to get help when issues arise, leading to potential delays in your production.
3. Warranty Issues: Warranty claims can sometimes be difficult to navigate. Depending on the manufacturer, you might face challenges when trying to claim a warranty or receive service, which could lead to frustration if problems occur.
How Long Do Chinese CNC Machines Last?
The longevity of a CNC machine depends on several factors, such as its quality, usage pattern, and level of maintenance. How long do Chinese CNC machines last?
Good Chinese CNC machines last a long time, especially when they come from reputable manufacturers. Some consumers report using their products for over ten years with proper maintenance. Regular maintenance can extend the life of any CNC machine. This entails cleaning, lubricating, and replacing worn-out parts. Most Chinese CNC machines come with maintenance guidelines that, if followed, can significantly increase the machine's lifespan.
A machine will wear down faster with increased use. However, a well-built Chinese CNC machine can endure for several years, even with severe use. A high-quality Chinese CNC machine may provide excellent value for money and a long lifespan with regular maintenance.
Final Thought
Many firms can benefit from using Chinese CNC equipment. They come in a variety of models, are reasonably priced, and are useful. Many additionally provide opportunities for customization to fulfill certain requirements. Selecting a reliable manufacturer is crucial because quality can differ.
Investigate your options because problems with customer service and warranties could come up. All things considered, a Chinese CNC machine can help you increase efficiency and expand your company with the appropriate strategy. You can choose a machine that is ideal for your needs by assessing the benefits and drawbacks.
1. Focus lens for contamination: Clean focusing mirror.
2. Focus relief laser engraving machine equipment whether changes: Re-adjust the focus.
3. Light path is offset: Carefully adjustment of the optical path.
4. Reflective lens is contaminated or damaged: Clean or replace the reflective lenses.
5. Laser power is energized: Checking laser power supply circuit so that it is normal.
6. Laser tube is damaged or aging: Replace the laser tube.
7. Laser power supply is damaged: Replace the laser power.
8. Cooling water is circulating flow: Clear cool water.
9. The cooling water temperature is normal or not: Replace the clean cooling water to the temperature to normal.
What I tell you about the laser weaker of laser engraving machine? we have to know how the above problems to be fixed, and welcome to our online support with laser engraving machine.
1. When laser engraving with gradient, double phenomenon.
This phenomenon occurs when the slope of words carved smaller, usually the reason is "wide" setting slope too large, cause calculation errors, please set "wide" little slope.
2. If you only can move a graphic with one direction, please click "Shift" or "Ctrl" to recover.
3. PLT format cannot to engrave.
There are two reasons, one is the graphic is not closed, the other is graphic double. Please detect this phenomenon with "data detect" tools.
4. The size is not same with laser engraving and cutting samples. Open the item "laser engraving machine set", adjust the pulse.
5. The edge is irregularity when laser engraving.
The edge is irregularity maybe happen when you use the DSP laser engraver software, that means "burr", this is mainly caused by mechanical return clearance, this is the solution.
a. Draw a box (rectangular or square), set work mode for the laser engraving machine, the sculpture is 0.5 mm instead, then see laser engraving effect, theoretically, should be aligned, namely the odd interlaces did edge should be aligned, even did edge also should be aligned, only the odd and even did not have a little.
b. When you open "set laser engraving parameters", the parameters for different. laser engraving speed can be seen, the reverse gap is "0", you should adjust it as the matter of fact.
c. You can choose "single-track light" when best laser engraving effect needed. Not to chose the draw of "dual-engrave", but when you chose it, the efficiency would be lower.
6. The X-axis or the Y-axis not move.
a. Stir knob to chose the DC 5V, test the voltage between PULX(or PULY)and GND. Take Y axis as example, click the button of "up" or "down", the normal voltage is 2.8V, if it is not, we could confirm the controller was broken, please change the controller. If it is, please go to next step.
b. Exchange the output terminal of the two drivers, then press "Up" or "Down" button; if X axis works normal, it means there is something wrong with the motor on Y axis, please change a new one; if X axis doesn't work, it means there is something wrong with the driver on Y axis, please chance it.
7. X Axis and Y Axis work in only one direction.
a. Test the voltage between the DIRX and GND after pressed the multimeter into grade 5V; take the X Axis for example, press "left", then press "right" to see if there is some change on high level (>2.8V) and the low level(<0.8V); if not, the control card is broken and need to change a new one.
b. If with change, please check the driver; if works normal, please change the driver on Y Axis.
8. NO Ray.
Test the voltage between the LAS and GND after pressed the multimeter into grade 5V; press "fixed fire" in the control panel, to see if there is some change on high level (>2.8V) and the low level(<0.8V); if not, the control card is broken and need to change a new one. Also set up the time of fixed fir as 0 millisecond, which is in the PAD03 menu.
Adjust the power from 0%~100%, enter and press "fixed fire" button, then test if any change between the DA1 and GND from 0V to 5V; if not, the control card is broken, please change it; if both with, it means there is something wrong with the laser power supply.
In modern days, laser cutters walk through everywhere in our lives and businesses, from small home stores to large industrial manufacturers, handling a variety of materials from soft fabrics to hard metals, and creating everything from simple lettering to complex 3D puzzles. Powerful yet easy to use for both beginners and professionals alike. Have you factored that into your business plan? Is this a cutting tool worth the money? Let's first explore the pros and cons of laser cutters.
Here's a balanced overview of laser cutter pros and cons, covering key factors for hobbyists, makers, and professionals:
? Pros (Advantages & Benefits)
Precision Cutting & Fine Engraving
Lasers are professional to create fine cuts and intricate engravings that are beyond the reach of most manual and mechanical cutting tools, making them ideal for complex designs, fine text, and detailed artwork.
Material Diversity
Lasers can engrave and cut a wide range of materials: wood (plywood, MDF, solid wood), acrylic (plexiglass), leather, fabric, paper, cardboard, rubber, stone, glass, stainless steel, carbon steel, copper, aluminum, alloys, and some composites. (CO2 lasers are best for nonmetal materials; fiber lasers are ideal for metal materials).
Clean Cuts & Edges
Lasers can create smooth edges in a variety of materials by setting power options, material properties, and cutting parameters, eliminating the need for post-processing steps such as polishing and grinding, saving time, effort, and material waste.
High Speed & Efficiency
Compared with manual cutting tools or CNC cutting machines, laser cutters are faster at cutting and engraving, making them popular for rapid prototyping and mass production.
Repeatability & Consistency
Once your design and setup are complete, each subsequent cut is exactly the same, making them ideal for batch manufacturing.
Non-Contact Process
The laser beam cuts without physical contact with the material, which is safe and reduces the possibility of material displacement or damage during the cutting process.
Automation and Software Integration
Laser cutting machines can work with most CAD/CAM software (such as Adobe Illustrator, CorelDRAW, AutoCAD, LightBurn), which makes it easy to create, modify and send designs to the controller.
Minimum Waste (Kerf)
The laser beam is very thin ("kerf"), which means less material waste than thicker cutting tools such as saw blades, especially in nested designs.
Flexibility
Easily switch between cutting and engraving on the same machine with a simple software change.
? Cons (Disadvantages & Limitations)
High initial cost
A reliable CO2 laser cutter (even a desktop cutter) is expensive to purchase, and even more so, industrial-grade fiber laser cutting machines can cost tens of thousands of dollars, requiring a huge investment.
Material restrictions
CO2 lasers are typically used for cutting non-metallic and metalloid materials, and perform poorly in metal cutting other than thin sheet metal. Fiber lasers are only allowed to cut metal.
Hazardous materials
PVC, PTFE, vinyl, polycarbonate, Teflon, and materials containing chlorine or bromine produce toxic fumes that are harmful to health. Never cut unknown plastics and foams.
Highly reflective metals
Aluminum, brass, and copper can reflect the laser beam and damage the laser generator (special fiber lasers are required to cut reflective metals).
Thickness restrictions
The power determines the laser cutting capability. Thick materials require high-power lasers.
Safety Hazards
Extreme fire risks
Laser cutting generates high heat, which makes it easy for unattended operation or improper settings to ignite the material being cut (especially fabrics, paper, and wood), requiring fire extinguishers and safe operating procedures.
Toxic Fumes
Laser engraving or cutting certain materials can produce toxic and hazardous fumes, requiring specialized exhaust fans and ventilation systems to ensure safe production.
Personal Injury
Eyes may suffer laser damage and skin may suffer laser burns if exposed to lasers of certain wavelengths and intensities, requiring appropriate shielding and laser safety glasses.
Operating Costs and Maintenance
Consumables such as CO2 laser tube, mirrors and lenses, nozzle, protective lens, ceramic ring, and auxiliary gas come with a limited lifespan and high replacement costs, and require regular cleaning, calibration, care and maintenance.
Learning Curve
A deep learning curve is required in terms of operation, maintenance, safety procedures, and mastering CAD design software and cutting parameter settings (power, frequency, speed, focal length).
Edge Characteristics
Taper
Laser cutting will produce a slight taper (wider top and narrower bottom), which is particularly noticeable on thick materials.
Scorching/Blackening
The edges of laser cut solid wood, plywood, MDF, and bamboo will be charred and darkened.
Heat Affected Zone (HAZ)
The area near the laser cut edge may discolor or deform due to heat, especially on plastics and some sensitive materials.
Optimal Settings
Extensive testing is required to find the optimal settings (power, speed, frequency, focus, air assist) for each specific material type and thickness.
Noise and Space
Laser cutting generates noise (air compressor, exhaust fan, laser operation), and large-size industrial laser machines take up a lot of space, requiring a reasonable layout of the workshop.
In Summary
Laser cutters are smart manufacturing tools for precision cutting and engraving of various metal and non-metal materials, with features such as fast speed, high accuracy, high repeatability and flexibility. However, they require a high initial investment (equipment and site), carry serious safety responsibilities (personal injury and fire), and require continuous learning and practice. If your business requires you to purchase your own laser cutter, weigh the pros and cons based on your specific business needs and budget, as well as your workspace and safety commitments, and make a decision. For occasional laser cutter users, using a local laser cutting service may be more appropriate.
Whether a laser cutter is worth the money depends entirely on your specific business needs and budget, as well as your frequency of use and goals. The following categories will help you decide:
✅ When is it worth buying a laser cutting machine?
High-volume production or commercial use
If you run a business (e.g., Etsy shop, auto parts, sheet metal fabrication, custom signage, prototyping, crafts, jewelry, art, and gifts) that requires consistent, precise cutting and engraving, a laser cutter can quickly pay for itself with its efficiency and scalability.
Hobbyist or Maker Wwho Laser Cuts Frequently
If you spend a lot of time and money outsourcing your laser cutting, or have complex projects that are difficult to complete with hand or machine tools (knife, saw), owning a laser cutter can save time and unleash your creativity.
Experiment with a variety of materials (e.g., wood, acrylic, leather, fabric, paper, and some metals with fiber lasers) and complex designs that are impossible to accomplish by hand.
Specific Material Needs
Essential for cleanly cutting/engraving acrylic, fine wood inlays, detailed leatherwork, or metal marking (with the right laser).
Space and Performance Match
You have ample, well-ventilated space (critical!), power needs, and a budget for the machine and basic accessories (extractor, compressor, air assist, cooling).
Technical Ability and Interest
You are comfortable learning the software (CAD, Illustrator, LightBurn) and performing basic maintenance (calibrating mirrors, cleaning lenses, troubleshooting).
❌ When is a laser cutting machine not worth owning?
Infrequent or Occasional Use
If you need laser cutting or engraving occasionally, but not often, outsourcing your business may be more cost-effective, saving you a series of tedious operations such as learning, purchasing, operation, and maintenance.
Tight Budget (with Hidden Costs)
Machine Cost: Laser cutters range from around $1,000 (entry-level models) to $6,000 (professional models) to $10,000+ (industrial models).
Must-Have Extras: High quality fume extraction ($200 to over $1,000), air assist (approx. $100 to $300), cooling system (CO2 water chiller - $150 to $500), replacement lenses/mirrors, honeycomb bed, and materials, all of which can easily double the initial cost of the machine.
Maintenance and Repairs: During the use of the machine, there should be regular constant care and maintenance, which should be considered in terms of ongoing costs.
Space and Ventilation Limitations
Lasers require a lot of space and must have proper ventilation (legal and safety aspects).
Material Limitations/Alternatives
Need to cut thick metal? A plasma cutter or water jet cutter is a more affordable option.
Need to cut thin paper, card stock, vinyl? Cricut and Silhouette are cheaper, quieter, and safer.
Need simple wood cutting? A good jigsaw or bandsaw will suffice.
Intolerable Hassle
Requires setup, calibration, maintenance, material testing, and troubleshooting. Not truly "plug and play" (except for the Glowforge, but that's more expensive).
Security Risks
Fire Risk: Never leave a laser unattended. Constant vigilance is required.
Toxic Fumes: Cutting certain materials (PVC, vinyl, certain treated woods) can release deadly fumes. Proper extraction is a must.
Eye Damage: Strict eye protection is a must (preferably an enclosure with an interlock).
?Key Considerations Before Buying
Budget: Actual total budget (machine + all accessories + materials + maintenance buffer).
Primary Use Cases: What materials are cut? What thickness? Cutting, engraving, or both? Production volume?
Space & Ventilation: Do you have a dedicated, well-ventilated workshop/garage? Can you install ducting?
Technical Skills: Are you good at debugging and troubleshooting software and hardware?
Time Commitment: Will you use these resources well enough to offset the cost/hassle?
Alternatives: Have you tried other cutting tools? Would a CNC router or vinyl cutter suffice?
?Recommendations
Calculate Outsourcing Costs: Estimate how much it would cost you to outsource your laser cutting work each year. How long would it take for a machine to pay for itself?
Try Before You Buy: Experience a laser cutter at a local dealer, makerspace, or friend’s studio before committing to a purchase.
Start Small: If you're a hobbyist, a powerful CO2 laser can be a low-risk starter option (about $1,200 to $3,600), but be aware of their limitations (slower, thinner, and primarily cuts non-metallic materials).
Research Relentlessly: Check online reviews (Amazon and Google), join forums (Reddit: r/lasercutting), compare specs, and learn about software.
Bottom Line
If you use it often enough to justify the high upfront investment and ongoing costs, and it unlocks features that are critical to your projects or business, then a laser cutter is definitely worth the money. If not, outsourcing or another tool is a smarter choice.
1. The machine and the computer must have a good grounding.
2. Open the cutting software, click the file menu, communication settings to receive and send the buffer time is changed to 5 or 10.
3. The replacement of the data line or motherboard.
According to the same direction of the panel button, the laser cutting machine appears to be turning and reversing and motor power can not be locked.
1. First disconnect all power supply, the high pressure head with cotton cloth to wipe clean. (gentle scrub)
2. Cut off the broken pipe, re received the laser tube. And bundled with a tie.
3. The high voltage line (high pressure line with 7 silver thread, one less).
4. The fan will dry high pressure wet place, after half an hour, and then boot.
1. CNC router spindle rotation sound is not normal
a. The drive is set incorrectly.
b. Check whether the cooling water circulation.
c. There are problems with the spindle (bearing damage).
d. If the noise when loaded knife, normal, replace the tool without tooling.
2. CNC router spindle hot or noisy:
a. Check whether the cooling water circulation.
b. Check whether the bearing problem.
c. If loaded knife noise, without tooling normal, replace the tool.
3. CNC router spindle cooling water does not flow:
a. Check the coolant pump is working properly.
b. Check whether the water flow, the water from the spindle joint apart, blowing to the other side of the steam gun from one side or the connector on the spindle with a needle penetrating.
4. Motor reversal:
Check the motor cable is phase output UVW terminal ends of any exchange.
1. Roughness
Laser cutting cross section will form a vertical lines, the depth of the texture of the cut surface of the roughness of the cut surface, the more shallow lines, the more smooth cut section. Roughness not only affects the appearance of the edges, but also affect the friction characteristics, in most cases, it is necessary to minimize the roughness, so the more shallow texture, the higher the quality of the cut.
2. Verticality
If the sheet thickness exceeds 10mm, the verticality of cutting edge is very important. Away from the focus, the laser beam becomes divergent, according to the location of the focus, cutting to the top or bottom of the variable width. Cutting edge off the vertical line of a few millimeters, the edge of the more vertical, the higher the quality of cutting.
3. Cutting width
Kerf width generally does not affect the cutting quality, only in the internal components formed special precision contour, cutting width is important. This is because the cutting width determines the contour of the minimum, when the plate thickness increases, the cutting width also increases. So want to guarantee the same high precision, no matter how much the width of the cut, the workpiece in the laser cutting machine processing area should be constant.
4. Lines
High speed cutting thick plate, the molten metal will not appear in the vertical laser beam below the incision, but will be sprayed out at the laser beam side. As a result, the curved lines are formed on the cutting edge, and the lines are closely followed by the laser beam. In order to correct the problem, the feed rate can be reduced at the end of the cutting process.
5. Burr
Burr formation is a very important factor to determine the quality of laser cutting, because the removal of burr need extra work, so the amount of burr is serious and how much is able to directly determine the quality of cutting.
6. Material Deposition
Laser cutting machine before the beginning of melting and perforation of the workpiece surface with a layer of oil on the surface of a special liquid. Gasification and all kinds of materials, the material does not need to use the wind to blow the cut, but the upward or downward discharge also can form the deposition on the surface.
7. Sag and Corrosion
Sag and corrosion have adverse effects on the surface of the cutting edge, affecting the appearance. They appear in the error of the cut which is generally supposed to be avoided.
8. Heat Affected Zone
In laser cutting, the area near the notch is heated. At the same time, the structure of the metal changes. For example, some of the metals can be hardened. The heat affected zone refers to the depth of the area that is changed by the internal structure.
9. Deformation
If the cutting makes the component heat, it will deform. This is particularly important in fine processing, because the profile and connecting pieces are usually only a few millimeters wide. Control of laser power and the use of short laser pulses can reduce the parts to become hot, to avoid deformation.
These days, a wide range of industries depend on plasma-cutting technology. It cuts through many types of metal quickly and precisely. Using a high-velocity plasma stream of ionized gas, the most recent technique melts the metal to produce clean, accurate cuts. Plasma cutting tables automate this cutting process, allowing operators to provide precise results with less human work. These tools are widely used in manufacturing, construction, and the car industry, among other sectors where efficiency and accuracy are vital.
It is important for anyone considering buying one of these equipment to be aware of the costs associated with plasma cutting tables. Size, power, and technology are some key elements that influence cost. This post will discuss the standard price ranges for several types of plasma cutting tables, the factors influencing these costs, and the variety of options available. After reviewing this article, readers will have a better understanding of what to anticipate when planning a budget for a plasma cutting table.
What is the Cost of Owning a Plasma Cutting Table?
While choosing a plasma cutting table, price is a crucial consideration. A few factors that could result in a wide range of prices are size, power, and features. To help you make an informed purchase, we'll examine the various price ranges and the variables that affect them in this section.
Entry-Level Plasma Cutting Tables
Entry-level plasma cutting tables typically cost between $2,000 and $5,000. These tables are appropriate for minor projects and light-duty activities. They frequently have manual controls and simple functionality.
Mid-Range Plasma Cutting Tables
The usual price range for mid-range plasma cutting tables is $5,000 to $15,000. These devices have more features and perform better. For companies who need to cut heavier metal and a greater range of materials, they are perfect. For more accuracy, mid-range models frequently have CNC capability.
High-End Plasma Cutting Tables
The price range for high-end plasma cutting tables is from $15,000 to over $100,000. These devices are built for heavy workloads and industrial applications. They have more sophisticated features like bigger work surfaces, faster cutting rates, and automated controls. The improved quality and technology utilized in its construction are reflected in the higher cost.
Additional Features That Affect Cost
High-definition cutting, integrated software, and sophisticated cooling systems are examples of extra features that can affect cost. Although these characteristics can improve effectiveness and performance, they may raise the table's total cost. When choosing the best plasma cutting table for their unique requirements, customers can make more educated judgments if they are aware of these price points and characteristics. It guarantees they receive the highest return on their investment.
Types of Plasma Cutting Tables Available in the Market
When choosing a plasma cutting table, understanding the different types available is essential. Each type is designed for specific applications and needs. Knowing these differences helps you select the right table for your projects and ensures optimal performance.
Manual Plasma Cutting Tables
The cutting torch on these tables must be manually controlled by the operator. Although they are typically less expensive, using them successfully takes more experience and ability. Smaller jobs and basic cuts are appropriate for manual tables. However, depending on the operator's expertise, the precision may vary and the learning curve may be steep.
CNC Plasma Cutting Tables
The cutting operation is automated by Computer Numerical Control (CNC) tables. They can create intricate designs and precise cuts because they use a computer to regulate the torch's movement. Due to their superior technology, CNC tables are usually more expensive. Their large volume production capabilities and ability to maintain consistency across many sections make them a popular choice in industrial environments.
Portable Plasma Cutting Tables
These are smaller and designed for easy transportation. They are ideal for fieldwork and smaller projects. While they are often less expensive, they may not offer the same cutting power as larger models. Portable tables are excellent for contractors who need flexibility on job sites and can handle various metal thicknesses within their limits.
High-Definition Plasma Cutting Tables
The greatest level of precision is offered by these advanced tables. They have characteristics that enable complex cuts on a variety of materials. But they are more expensive; they frequently cost more than $30,000. For businesses like aerospace and automobile manufacturing, where even small errors can have serious consequences, high-definition plasma tables are ideal.
Popular Plasma Cutting Table in the Market
Small Entry-Level 4x4 CNC Plasma Table
The STP1212 from STYLECNC is an entry-level CNC plasma table with a 4x4 working area, which is designed for hobbyists seeking precision cutting capabilities in metal fabrication. The 4x4 plasma cutting table comes with a rugged construction to ensure durability and stability during operation, while the user-friendly software makes it easy for beginners to use. Overall, this small plasma cutting table is considered a great and affordable investment for DIYers and artists, whether they are looking to improve their metalworking capabilities or increase their creativity and productivity in metal fabrication.
Top Rated Professional 4x8 CNC Plasma Cutting Table
The best 4x8 CNC plasma cutting table of 2024 from STYLECNC is designed for professionals working on precise sheet metal cutting with a 48" x 96" bed size. It supports various power options, including Hypertherm and Huayuan, with cutting capacities up to 40mm. The machine features a Starfire control system, automatic torch height control (THC), and FastCAM software for material-saving nesting.
Its sawtooth or blade table design ensures stability, while optional rotary devices allow for metal tube cutting. The table offers high precision, versatility, and efficiency, making it ideal for industries such as fabrication, automotive, marine, and signage. Regular maintenance and proper calibration ensure long-term performance and productivity.
Industrial 5x10 Hypertherm Plasma Cutter Table
The 5x10 Hypertherm plasma cutter table from STYLECNC is a high-performance machine designed for precise and efficient metal cutting in industrial manufacturing. It features a 1500x3000mm cutting table and supports rotary cutting of pipes with diameters from 200mm to 600mm. Powered by options like Hypertherm Powermax (45A to 200A) or Huayuan, it can handle materials up to 40mm thick. The machine integrates a Starfire CNC control system, HYD torch height controller, and dual-motor Y-axis drive with Taiwan Hiwin linear rails for smooth and precise operation.
The advanced features of STYLECNC's plasma cutting table include lubrication systems, auto-fume extraction, and flexible configurations for both sheets and tubes. Its high speed, robustness, and reliable performance make it perfect for use in industries such as aerospace, manufacturing, and shipbuilding. To improve operator safety, safety features like emergency stops, voltage monitoring, and thermal overload protection are included. It provides thick metal manufacturing at a lower cost with optimal energy consumption when compared to fiber laser cutters.
Factors That Influence the Cost of Plasma Cutting Tables
Several factors can affect the cost of a plasma cutting table. Understanding these can help buyers find the right machine for their needs.
• Size of the Table: Larger tables can accommodate bigger sheets of metal. They generally cost more due to their size and increased capabilities.
• Power Requirements: Plasma cutters come in various power ratings, which affect cutting speed and thickness. Higher power machines are more expensive but offer greater cutting capabilities.
• Brand Reputation: Established brands often charge more for their machines. However, they typically provide better quality and reliability, making them a worthwhile investment.
• Additional Features: Features like CNC automation, advanced software, and improved cooling systems can increase the price. Buyers should assess which features are essential for their work.
Additional Costs to Consider
In addition to the initial purchase price, there are other costs to consider when buying a plasma cutting table. Understanding these expenses can help you plan your budget effectively.
Software
Many machines require specialized software for operation. This can range from $500 to $5,000, depending on the capabilities. The right software can significantly enhance the cutting process, enabling more complex designs and better precision. Investing in high-quality software ensures you get the most out of your plasma cutter.
Maintenance
Sufficient performance requires routine maintenance. This involves changing out wearable components like electrodes and nozzles, which raises continuous expenses. Maintaining your machine not only makes it last longer but also makes sure it runs well. Ignoring maintenance can cost you money in repairs and cause downtime, which lowers production.
Consumables
Plasma cutting requires consumable materials that need regular replacement. Budgeting for these can help avoid unexpected expenses. Consumables can include electrodes, nozzles, and plasma gas, all of which are necessary for effective cutting. Keeping a close eye on your inventory of consumables ensures you won’t face interruptions during critical projects.
Accessories
The price of the item may also increase with additional accessories like toolboxes, clamps, and safety equipment. You should account for these in your budget. To shield personnel from potential risks during the cutting process, safety equipment is essential. Good clamps and toolboxes can improve productivity and coordination, which will improve workspace efficiency overall.
Is Buying a Used Plasma Cutting Table a Good Option?
Buying a used plasma cutting table can be an appealing option for many businesses. It offers a chance to save money while still acquiring a valuable piece of equipment. However, it is important to weigh the advantages and disadvantages before making a decision.
Pros of Buying a Used Plasma Cutting Table
• Cost Savings: Used machines are typically cheaper than new ones, allowing buyers to access higher-quality models without breaking the bank.
• Less Depreciation: Purchasing a used machine often means experiencing less depreciation, helping you maintain more of your investment over time.
• Opportunity for Upgrades: With the savings, you may afford a more advanced model or additional accessories, enhancing your overall capabilities.
Cons of Buying a Used Plasma Cutting Table
• Wear and Tear: Used machines may show signs of wear, which can impact performance and cutting precision, leading to unexpected maintenance costs.
• Outdated Technology: Older models may lack the latest features and capabilities, hindering productivity in a fast-paced industry.
• Limited Warranty: Used machines often come with limited or no warranties, increasing the risk if something goes wrong shortly after purchase.
Before buying a used plasma cutting table, it is crucial to conduct a thorough inspection. Understanding the machine's history, previous usage, and maintenance records can help you make an informed decision. By weighing these pros and cons, you can determine if a used plasma cutting table is the right option for your needs.
Final Words
It's important to carefully examine your goals and budget while selecting the best plasma-cutting table. Determine the kinds of materials you plan to cut and the amount of work you anticipate before beginning. Entry-level variants of plasma cutting tables typically cost $2,000, while high-end industrial units can cost over $100,000. It's critical to assess your budget and account for any supplemental expenses for consumables, maintenance, and software.
Investing in a well-chosen plasma cutting table can significantly boost productivity and efficiency. By taking into account the costs and features, together with any potential savings from buying used equipment, you can make an informed choice. Knowing what types are available and what their price ranges are will help you choose a table that meets your needs without going over your budget. Your cutting operations will operate profitably and efficiently over the long term if you make wise investments.
Laser engraving or laser cutting is to converge the laser beam into a small spot through a focusing mirror and project it onto the surface of an object. The focal point reaches a high power density. At this time, the irradiated part of the material is quickly heated and vaporized, and the laser beam and the material move relatively linearly, so as to realize laser engraving cutting plans.
When the laser engraving machine or laser cutting machine is working for a long time, the optical path will deviate, which will affect the cutting effect. Only the perfect cooperation of laser tube, reflecting mirror frame (A, B, C), focusing lens and corresponding adjustment device can achieve the best effect and process the best projects. This is the core part of using CO2 laser machine. Therefore, it is very necessary to check the laser beam path and adjust it regularly.
8 Steps to Adjust and Align CO2 Laser Beam Path:
1. Turn on the air pump, the air flow is discharged under the trolley, and the wires on the X and Y axis drives of the right control box are pulled away.
2. Turn on the machine switch, the LCD display on the operation panel shows "The system is starting, please wait ..." At this time, the machine is in the reset state, wait for about half a minute, then the LCD displays: File name: AAA Processing speed 100% processing Power: 100/100% Processing quantity 1 Delete. At this time, the machine is in the initial online state.
3. Stick a round cardboard larger than the lens in front of the first reflective lens and the second reflective lens.
4. Put a large cardboard in front of the laser head of the tube, press the fire button on the operation panel, the laser tube emits light, and adjust the laser to the first reflection by adjusting the front and rear positions of the laser tube bracket and the thickness of the rubber under the tube The middle of the lens.
5. Adjust the laser to the middle of the second reflective lens by adjusting the three screw shafts behind the first reflective lens. When adjusting the second reflective lens, the X-axis beam should be moved to the front and back, the point where the laser hits Be completely coincident.
6. Adjust the laser to the hole on the left side of the laser head by adjusting the three screw shafts behind the second reflective lens. When the laser head moves to the four corners of the worktable, the laser must hit the middle of the hole.
7. Focus adjustment.
Focal length refers to the distance (4-4.2mm) between the top of the cone head under the laser head and the surface of the material.
8. By adjusting the tightness of the three screws on the mirror above the laser head, the laser can be adjusted to the vertical angle to ensure the verticality of the cutting surface when cutting.
Portable CNC machines have become a must-have tool for hobbyists, small business owners, and professionals who need precision and mobility in one compact package. These machines are designed to be easy to transport while still delivering the same level of accuracy and quality as their larger counterparts. Whether you're working on-site, in a small workshop, or need flexibility for various projects, portable CNC machines make it possible to tackle a wide range of tasks without taking up too much space.
In this article, we'll dive into the key features that make a CNC machine truly portable and why these machines are perfect for small-scale projects. We’ll also explore how they compare to larger models in terms of precision, and their impact on the manufacturing industry, and provide tips on choosing the right machine for your needs. Ready to explore the world of portable CNC? Let’s get started!
What Makes a CNC Machine Truly Portable? Key Features to Look For
When you're in the market for a portable CNC machine, it's important to know what specific features make a machine truly portable without sacrificing precision or functionality. A portable CNC machine should not only fit into your workspace but also be easy to move from one job site to another. For professionals working in various locations, having a lightweight and versatile machine that doesn't compromise on quality can make all the difference. This guide covers the essential features that ensure portability while maintaining the high standards needed for CNC operations.
Knowing about the key features that define a portable CNC machine will help you make an informed decision, whether you're setting up a mobile workshop or need flexibility for on-site work. Below, we break down these features and why they matter when choosing the right machine for your needs.
Key Features to Look for in a Portable CNC Machine
• Compact Design and Lightweight Build: Portability starts with the design. A CNC machine that’s easy to move around should have a compact structure that doesn't take up much space. Choose a machine made with lightweight materials that offer durability without the weight, making transportation easier.
• Power Source Flexibility: Being able to use the machine in various locations requires flexibility in power options. Look for machines that can run on standard electrical outlets or even have the ability to work with alternative power sources like batteries, making them adaptable to remote work environments.
• User-Friendly Interface: A portable CNC machine should have an intuitive interface that makes operation simple, even for beginners. Easy-to-navigate software and controls are essential for making quick adjustments and ensuring smooth operation when you’re on the go.
• Durability and Robustness: Even a portable machine needs to be tough. Check for solid construction, such as a sturdy frame, that can withstand the rigors of frequent movement. A durable CNC machine ensures that even in transit, it will maintain accuracy and longevity.
• Quick Setup and Tear Down: Look for machines that can be set up or packed away quickly. The more efficient the setup process, the less time you spend on prep and teardown, especially when moving between jobs or locations.
• High Precision in a Small Package: A portable CNC machine should not sacrifice precision for portability. It’s crucial that even in a smaller form, the machine delivers the same level of accuracy as its larger counterparts to ensure your projects meet professional standards.
Top Benefits of Using a Portable CNC Machine for Small-Scale Projects
Portable CNC machines are designed to be compact, lightweight, and highly efficient, making them the perfect choice for those who need precision and mobility without sacrificing quality. Whether you’re a hobbyist or a small business owner, portable CNC machines can improve your workflow and save you time and resources. Let’s explore the top benefits that come with using these machines for your small-scale projects.
Increased Flexibility and Mobility
Portable CNC machines allow you to work in different environments, whether it’s a workshop, an on-site project, or at a client’s location. This flexibility helps you take on a wider range of jobs without the need for a large, permanent setup, making it easier to meet the demands of your customers.
Cost-Effective Solution
For small-scale projects, investing in a portable CNC machine can be more affordable than traditional larger machines. They offer the same high-level precision and efficiency but at a fraction of the cost, making them an ideal solution for businesses with a limited budget or hobbyists just starting.
Space-Saving Design
Portable CNC machines are compact and can be stored easily when not in use. If you have limited space in your shop or workspace, a smaller CNC machine allows you to maximize the area available without compromising on your project quality.
Ease of Use and Setup
Most portable CNC machines are user-friendly and require minimal setup time, allowing you to start working right away. This can be especially beneficial for small-scale projects where time is of the essence, helping you complete tasks faster and with fewer hassles.
Precision and Quality in Small-Scale Work
Despite their small size, portable CNC machines maintain the same high level of precision as their larger counterparts. Whether you’re cutting wood, plastic, or metal, these machines ensure that your small-scale projects are executed with accuracy and attention to detail, leading to professional results every time.
Reduced Overhead Costs
Since these machines are portable and versatile, you can use them for a variety of tasks without needing to invest in multiple machines. This helps reduce overhead costs, as you don’t have to purchase specialized equipment for each job.
Are Portable CNC Machines as Accurate as Their Larger Counterparts?
Portable CNC machines have gained popularity for their flexibility and compact design, but one common question that arises is whether they can match the precision of their larger counterparts. While portable CNC machines may not have the sheer size and power of industrial models, they can still deliver exceptional accuracy for most small-scale projects. Thanks to advancements in technology, many portable machines are designed to achieve high precision levels comparable to larger machines.
These machines often use advanced control systems, high-quality spindles, and precision components that enable them to perform intricate tasks with minimal error. For many tasks such as engraving, small part cutting, and detailed carving, portable CNC machines can offer results that are just as accurate as larger models, all while being more cost-effective and space-efficient.
Consistent Precision with Smaller Jobs
Portable CNC machines are ideal for smaller-scale operations and can handle intricate designs with impressive accuracy. They are built to cut, carve, and engrave on various materials with a high degree of precision, making them perfect for hobbyists, makers, or small businesses focusing on detail-driven projects.
Ideal for Prototyping and Custom Work
Portable machines are often used in prototyping and one-off custom jobs where precision is crucial. They can produce parts with tight tolerances that meet the needs of industries such as jewelry, custom signage, and electronics.
Precision Technologies Used
Modern portable CNC machines come equipped with features like high-precision stepper motors, ball screw mechanisms, and advanced CNC controllers. These components contribute to achieving better accuracy, even in machines that are smaller and lighter than their industrial counterparts.
The Impact of Portable CNC Machines on the Global Manufacturing Industry
Portable CNC machines have made a significant impact on the global manufacturing industry, offering benefits that were once exclusive to large-scale operations. These compact machines provide manufacturers with flexibility, cost-efficiency, and access to precision in ways that were previously out of reach for smaller businesses or individual makers.
One of the key advantages is the ability to work on-site or in smaller workshops, eliminating the need for expensive industrial setups. This has democratized manufacturing, enabling startups and small businesses to enter the market without hefty upfront costs. Additionally, portable CNC machines allow for faster prototyping, which is essential for industries that require rapid iteration, like product design and innovation.
They’ve also improved accessibility for manufacturers in remote or underserved regions, reducing the dependency on large factories. This accessibility fosters local production, helping to shorten supply chains and reduce lead times. Overall, portable CNC machines have shifted the dynamics of the manufacturing industry, enabling more businesses to compete on a global scale and helping speed up production processes in diverse industries.
How to Choose the Right Portable CNC Machine for Your Needs?
Choosing the right portable CNC machine for your needs can be a game-changer, whether you're a hobbyist, small business owner, or part of a larger operation. The right machine will offer precision, efficiency, and versatility without taking up too much space or breaking the bank. Here’s how you can approach the selection process step by step:
Step 1: Define Your Project Requirements
Before diving into specifications, take a moment to consider the materials you'll be working with, the complexity of your designs, and your desired production speed. Are you primarily cutting wood, metal, or plastic? This will guide you toward the right machine.
Step 2: Consider Size and Portability
Since you’re looking for a portable CNC machine, its size and weight should be top priorities. Check if it can fit in your workspace while still offering the capacity to handle your projects. A compact yet robust machine can help you work efficiently without sacrificing mobility.
Step 3: Look at the Machine’s Precision and Accuracy
Precision is key in CNC work. Make sure the machine you choose provides the level of accuracy you need for your designs. Check the specifications for repeatability and resolution to ensure it can handle the intricacies of your projects.
Step 4: Evaluate the Control System and Software Compatibility
Look for a machine with an easy-to-use control system that works well with your preferred CAD/CAM software. User-friendly interfaces and software compatibility can significantly reduce the learning curve and improve your workflow.
Step 5: Assess Power and Performance
Portable CNC machines come with varying power ratings. Ensure the machine has the right motor power and speed to meet your production needs. A machine that strikes the right balance between power and efficiency will make your projects run smoothly.
Choose a brand with a strong reputation for customer service and support. A good warranty and after-sales support can save you time and money in case of any issues down the line.
The Limitations of Portable CNC Machines and How to Overcome Them
Portable CNC machines are a fantastic choice for many small-scale and home-based projects due to their compact size and versatility. However, like any technology, they do come with certain limitations that users should be aware of. One of the most common challenges is the limited workspace or smaller cutting areas compared to larger, industrial models. This can restrict the scale of the projects you can tackle, especially when working with larger materials or more complex designs.
Additionally, portable CNC machines may have lower motor power and cutting speeds, making them less suitable for heavy-duty or high-volume production. Precision might also be a concern, as smaller machines may not offer the same level of repeatability and fine detail that larger machines can provide. Finally, the complexity of programming and limited support for advanced CAD/CAM software may make it harder for users to optimize their machines for specific needs.
Despite these limitations, there are effective ways to overcome these challenges and ensure your portable CNC machine remains productive and efficient. Here are some solutions:
• Maximize Workspace Efficiency: Utilize rotating or adjustable fixtures to handle larger materials in smaller spaces, or consider investing in modular CNC workstations that can be expanded as needed.
• Optimize Cutting Speed and Power: Choose a machine with variable speed and power settings to adjust based on material type, and keep the cutting speeds within recommended ranges to avoid overload.
• Upgrade Precision: For more detailed work, consider investing in high-quality tools and accessories designed to enhance precision, such as precision collets, higher-grade motors, and rigid machine setups.
• Enhance Software Compatibility: Use compatible CAD/CAM software that integrates seamlessly with your portable CNC machine to maximize its capabilities and ensure smooth programming and workflow.
• Regular Maintenance: Perform regular maintenance, such as cleaning the machine, lubricating moving parts, and checking for wear and tear to ensure the machine operates at peak performance.
Note: If you can't find your answer in the FAQs above, please ask a new question in the form below.
Ask Your Question
Asking questions is essential in CNC machining for fostering understanding and encouraging exploration, allowing individuals to gain deeper insights and challenge assumptions, ultimately facilitating learning and innovation.