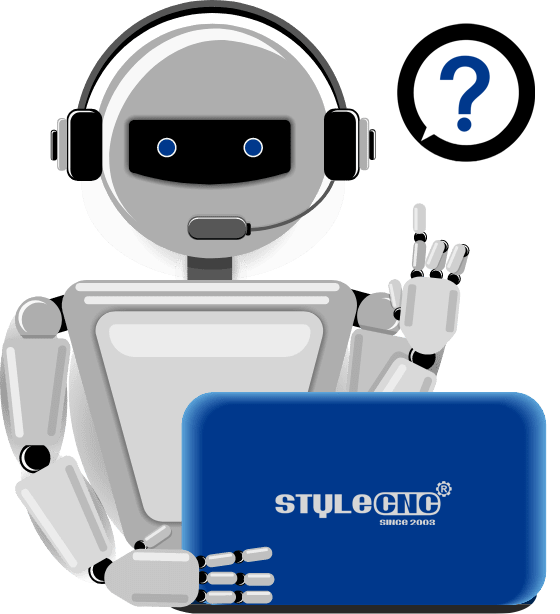
We typically build CNC machines to standard designs, however in some cases we can provide custom services as listed below.
1. Table sizes can be larger or smaller depending on your specific CNC machining needs.
2. Your logo can be put on the machine whether you are an end user or a dealer.
3. The appearance and color of the machine are optional according to your personal preference.
4. Individual machine specifications can be designed in a customer-oriented manner.
A CNC woodworking machine is a computer-controlled power tool that automates woodcuts, shaping, and drilling. It follows a program with instructions on what to do, hence it's accurate and repeatable in the work it does. These machines are widely used to create detailed, intricate designs and do detailed work on wood.
The typical machines contain a router, mill, or lathe on multiple axes of movement. With the computer controlling movement, the cuts are very accurate. This means that no labor by hand is required, and this makes woodworking much faster and more efficient.
CNC machines can be used to make small projects or for full-scale production. They can perform complex cutting tasks, 3D carvings, and engraving with ease. From a hobbyist to a professional, adding a CNC machine to one's woodworking capability will dramatically increase the volume.
How Much is a CNC Machine for Woodworking?
The cost of a CNC woodworking machine can vary greatly due to several variables associated with the machine's size, features, and brand. Here is a breakdown of general pricing into categories below.
CNC Machines for Beginners
Entry-level routers are rather inexpensive to get started with. The more basic models start at around $1,500 to $5,000. Most entry-level models are usually designed to meet the needs of a hobbyist or a small business. Typically, they come with a small area and only basic functionality. These can perform simple wood working tasks like engraving, carving, and light cutting.
Mid-Range CNC Routers
Precision and bigger, mid-range capabilities may run from $5,000 up to 15,000 dollars. This higher class of machines will have a greater working area and more power, making them ideal for companies that are in the small to medium-sized business range. They also often times include more sophisticated controls and automation such as auto tool changers and better spindle motors.
Industrial High-End CNC Machines
The prices for industrial-grade CNC routers range from $20,000 to over $120,000 at the high end. These machines are built for high-volume production, with larger workspaces-often greater than 4x8 feet. Advanced features include 5-axis capability, automation, and specialized software that enables the performance of specific tasks such as nesting and cutting complex shapes. Machines in this category would find use with large manufacturers or by companies manufacturing custom furniture.
Other Considerations
Besides the base price of a CNC machine, added expenses for software, tooling, installation, and maintenance can add literally thousands of dollars to the investment. Another huge determinant of price is whether a new or used machine is in question.
Price Factors of Woodworking CNC Machines
The cost of a CNC machine for woodworking depends on many factors. Knowing these factors will enable you to make an appropriate decision when buying a machine that suits your budget and needs.
Machine Size and Work area
The more enormous the machine and the wider its work area, the more it will cost. For example, a 4x8-foot CNC is going to be more expensive than a small one because it would require more material and components to assemble the machine. Thus, the machine will also allow you to work on more oversized pieces, in case you are after high-volume production.
Precision and Accuracy
The higher the accuracy and precision of the CNC machine, the higher the price is. Improved spindles, better ball screws, and high-quality linear guides are what build high-end models, providing accurate cuts with minimum maintenance. For intricate designs required to produce high-quality output--especially for professional woodworking--accuracy should be a top concern.
Features of the Machine
Advanced features such as multi-axis controls (e.g., 5-axis), automatic tool changers, and improved integrations with enhanced software greatly increase the price. These features allow the performance of more complex tasks, improving productivity by reducing human labor, hence becoming quite vital for large-scale production and thus adding to the cost.
Material and Build Quality
Materials used for building the CNC machine also determine the price. Machines made from high-quality steel or aluminum tend to be more expensive than ordinary ones. The quality of the build is affected in relation to durability, reliability, and long-term performance.
Brand and Manufacturer
The brand is probably the most factor in determining the price of any CNC machine. Renowned brands with a history of excellent, reliable machines can command high prices because they have earned reputations. Less well-known brands may offer less expensive versions, but they will not be as precise or last as long.
Various Types of CNC Machines and Price Tags
There are several types of CNC machines for woodworking, ranging from simple to complex and thereby fitting different needs and budgets. A look at the main types of CNC machines and their costs follows.
CNC Routers
Of the various available types of CNC, most popularly used in woodworking are the routers. These machines are designed to perform different operations on woods, plastic, and other materials. They may be as small as those used for small projects or as huge as industrial CNC wood routers intended for large-scale productions. Prices for these types of CNC wood routers range from a low-end estimate of $1,500 up to 120,000 dollars or even higher, depending on the size of the machine, features, and its intended application.
CNC Mills
CNC mills are utilized for intricate and precision cutting and can be employed on harder materials like metals, plastics, and wood. Less commonly used for woodwork, they are appropriate when high accuracy with versatility is required. CNC mills have vertical and horizontal configurations. Prices run from $10,000 to $150,000, with vertical mills costing less as opposed to the horizontal mills.
CNC Lathes
CNC lathes are used for turning wood or other material into cylindrical shapes. They will perform good tasks such as spindle turning, where the material spins while a cut tool shapes it. These machines are usually more specialized in types of woodworking projects. Costs vary with capabilities and size but range from $3,000 to $50,000 for CNC lathes.
3D CNC Printers
Though less traditional, 3D CNC printers are gaining in popularity for woodworking applications. In this case, they are mostly used for printing models, prototypes, and other complex designs. These work simply by layering materials, including the wood filaments. The cost of these 3D CNC printers will be from $2,000 up to $50,000 depending on the print size and technology involved.
Laser CNC Machines
Laser-cutting CNCs are also commonly used to cut and engrave finer details in wood. These machines use a focused laser beam to perform cuts, so they are very accurate. Prices range from $3,000 to $30,000 depending on the power and capability of the machine.
Low-End vs. High-End CNC Machines for Woodworking
When choosing a CNC machine for woodworking, you’ll come across both entry-level and high-end models. Each type has its advantages, depending on your needs, budget, and the complexity of your work.
Entry-Level CNC Machines for Woodworking
The entry-level routers are good to go for hobbyists and small businesses. These machines can be much cheaper, in the range of 1,500-5,000 dollars. They have smaller work areas and less complicated features, yet they are capable of performing basic operations of carving, engraving, and even cutting. They operate easily and are good for first-time users but might not be powerful enough or highly precise for larger projects that are more complex in nature.
High-End CNC Machines for Woodworking
High-end CNC machines range from 20,000 to 120,000 dollars or more and are industrial-level, featuring larger workspaces, advanced features such as 5-axis capability, and higher precision. They operate faster and more reliably in high-volume production for complex cuts on large projects using thicker materials.
Choosing Between the Two
Entry-level machines will do for beginners or smaller projects, but when you want to grow your business or need precision at a higher quality, then invest in a high-end machine that can carry all the tools needed for growth.
Selecting the Right CNC Machine for Your Budget
Choosing the appropriate CNC machine for your woodworking business or hobby is of critical importance for gaining full value from your investment with a minimum financial burden. Some of the key considerations would include the following.
Establish needs and projects
Before deciding on purchasing a CNC machine, first of all consider the projects you will be working on. If you are looking at light jobs like engraving or carving small wooden pieces, then a basic model may also work. But if you aim to cut larger pieces or just cut with more complex designs, you will need a machine capable of higher functionality: a larger work area, 3-axis, or 4-axis movement.
Set Your Budget
These costs range from a couple of thousands of dollars to tens of thousands of dollars. It is important to have a clear budget because it will narrow down your options. High-end models offer more features, but most entry-level machines can do the basic functions for a fraction of the price. For the overall budget determination, consider other costs such as software, tooling, and maintenance.
Size of Machine/Workspace
Keep in mind the size of the material you are going to deal with. If it is a small signage or intricate carvings, a small machine with a 2x3 feet workspace would do just fine. On the other hand, if you want to cut a full sheet of wood or larger items, you would need a larger machine with at least a 4x8 feet or larger workspace.
Long-Term Investment
While entry-level machines might be affordable, higher-grade models can outperform them any time in terms of durability and versatility. It could be the case that your business or hobby will grow, requiring a much stronger machine later on. Consider the return on investment over the long term when weighing cheaper versus more expensive options.
Is It Worth It to Invest in a CNC Machine for Woodworking?
Investment in a CNC wood machine depends on your business's needs and objectives. These machines will raise the output level, accuracy, and consistency for hobbyists or small-time users. A CNC machine will change the workload from manpower dependency to automation of repetitive tasks and get more time for design and creativity.
Additionally, CNC machines can be flexible for you to make more complex and custom designs that may be difficult and time-consuming if made by hand. This, in turn, may mean more quality products and higher efficiency for your company, translating to better profit margins.
On the other hand, the CNC machines are quite expensive to buy, and as such, the ROI would be a little later. Therefore, weighing the costs involved in buying, operating, and maintenance of the machine is important against possible benefits.
Why Should You Choose From STYLECNC?
STYLECNC has been at the forefront of supplying CNC machines for more than 21 years, giving creative and reliable cutting solutions. The brand is well-recognized for its high-quality products matching the demands of both small businesses and hobbyists. They focus on providing excellent customer support, always ready to assist one in case of questions or concerns.
STYLECNC understands the importance of finding the right machine. Whether you need an affordable, computer-controlled tool or more advanced equipment for your business, their team offers personalized guidance to help you choose the best one. In addition, with STYLECNC, you will have much more than just a machine-you'll be given special support to enable your success.
Laser cutting technology has advanced the cutting methods and precision ever more than before. The cutting is done using a concentrated laser beam at high temperature. This technology is welcomed in almost every industry. The versatility of the machines makes laser cutting more popular and outstanding.
It features the usability of a wide range of materials to shape, carve, or engrave. But in particular, plastics require more attention while making a project with them. Yes, Laser cutting polycarbonate is possible. You just need to know how to find the best suit for your project and fix the machine properly with accurate parameters.
Today, we are going to discuss the versatility of laser cutting technology and how to use it most efficiently. We are also going to break down the fact if laser cutting polycarbonate is possible or not, and if possible how to do that. Let's dive into the mastery of manufacturing cutting tools.
What is laser cutting?
Unlike traditional cutting and sawing methods laser cutting introduces a high-temperature laser beam-cutting tool that offers the most precise and efficient manufacturing outcome. The laser is usually focused and controlled through CNC router machines.
There are two common types of lasers used for the job.
1. Carbon Dioxide (CO2) lasers and
2. Neodymium-doped yttrium aluminum garnet (Nd:YAG) lasers.
The CO2 laser is suitable for non-metals like wood, acrylic, and fabric. On the other hand, Nd: YAG lasers are used for cutting metals and are capable of higher power outputs.
Laser cutting is used on a wide range of materials (metals and non-metals). Currently, laser cutting is available for cutting, engraving, or shaping steel, aluminum, copper, wood, acrylic, plastic, leather, fabric, rubber, etc.
Is it safe to laser-cut polycarbonate?
Laser cutting polycarbonate can be done with caution since many plastics are not suitable to cut using heat. It is important to know what kind of plastic you are going to cut.
The thickness and material density also impact the cutting. All plastics are not recommended to be cut using a laser. Specifically talking about polycarbonate, they cut very poorly and often discolor and catch fire. Usually, this material is found as sheets. For some specific reason laser cutting polycarbonate is not recommended for all purposes.
Therefore, due to the lesser effectiveness of laser on polycarbonate, it is considered a poor choice to use laser cut. But if necessary and with better thickness laser cutting polycarbonate is possible. Let’s see what are the potential difficulties to face while laser cutting polycarbonate.
Challenges of laser cutting polycarbonate
Polycarbonate tends not to work out with the laser cutting method. Yet you can get your job done only by following precautions and proper steps. But first, let’s find out the various challenges to face while laser cutting.
✔ Generation of hazardous fume: High high-powered laser beam can generate toxic gases like carbon monoxide and hydrogen cyanide. In the absence of proper ventilation, this can cause severe health conditions.
✔ Material sensitivity to heat: Polycarbonate is sensitive to heat. Extra heat can cause this material to melt, burn, or undesirable surface.
✔ Potential for thermal stress and warping: Thermal stress is common with overheating laser beams. This often leads to discoloration and distortion of material. It also affects dimensional accuracy and fit of the final product.
✔ Difficulty achieving clean edges: Achieving clean and smooth edges is challenging while laser cutting polycarbonate. Initially, the edges are prone to melt and tend to regain their shape. Meanwhile, the edge loses smoothness and shape.
✔ Effects of additives and coatings: Polycarbonate sheets with additives and coatings come with more challenges. When the material is heated these additives and coatings produce additional toxic gases and bi-products.
Besides, the risk of surface damage, the complexity of parameters optimization, and regulatory compliance and safety standards are a few factors that face additional challenges.
The best way to cut polycarbonate
Unlike laser cutting, there are more effective cutting methods for polycarbonate. The best way to cut polycarbonate depends on several factors such as thickness, desired precision, etc. We have gathered a few ways considered most effective in cutting polycarbonate. Let’s find out which works best for you.
B. CNC Router
C. Table Saw
D. Jigsaw
E. Score and Snap Method and
F. Waterjet Cutting
They are proven useful with fewer challenges and better precision to a certain extent.
Safety Precautions
Plastic materials are not eco-friendly materials for our environment. Yet versatile composition makes them useful in many industries. Cutting polycarbonate using laser cutting technology requires special safety precautions.
The safety precautions need to be improvised actively. Here are a few key safety considerations,
✔ Proper ventilation is a must to remove toxic gases and contaminants. Use an exhaust system to remove fumes effectively.
✔ Use the suitable equipment only to maximize the smoothness and accuracy of the shape.
✔ Try to use polycarbonate sheets specifically made to laser cut. Take necessary steps if additives or coatings are available on the sheet.
✔ Wear an appropriate PPE set at work. Make sure your PPE comes with gloves, masks, and protective clothing.
✔ Fire safety is very important in laser-cutting polycarbonate. Keep a fire extinguisher nearby. Keep the flammable objects at a distance.
✔ Dispose of plastic waste properly.
Tips to cut polycarbonate efficiently
Cutting polycarbonate can be difficult in certain work environments. However, a few tips can come in handy. Try them out to get better results.
1. Select the right tools
Choose the appropriate cutting tools based on the thickness of the sheet. Use a table saw on thin sheets and jigsaw for curved or irregular cuts.
2. Use proper cutting techniques
Fix the sheet properly on the bed to avoid chipping or cracking. When using table saw use clamps to secure the sheet. Using a jigsaw? Move it slowly and steadily.
3. Optimize cutting parameters
Considering thickness adjust the cutting speed, feed rate, and blade speed. Try different settings to find the optimal balance.
4. Minimize heat buildup
Avoid excessive friction using sharp-edge tools. This will reduce the overheating issue. Apply cutting lubricants or cooling agents for more effective results.
5. Protective measures
Wear proper PPE set and use a dust mask.
6. Clean up
Remove debris and wastage immediately. Use sandpaper to bring smooth and clean edges.
How to clean discolored polycarbonate after laser cutting
Laser-cutting polycarbonate usually results in discoloring. Not following the proper usage instructions results in this discoloration problem!
Now, what are you going to do once the product comes with discoloration? We have given you a few ideas that may improve the final result. You can follow them step by step to get rid of this unwanted condition.
⇲ Allow the material to cool
⇲ Gently remove surface debris
⇲ Prepare a cleaning solution
⇲ Apply the cleaning solution
⇲ Rinse thoroughly
⇲ Buff with polishing compound
⇲ Check and repeat if necessary
You can apply a protectant additionally to prevent future discoloration.
Fiber laser cutting polycarbonate
Fiber laser cutting is more popular among consumers for cutting polycarbonate. A suitable polycarbonate sheet can ensure an efficient cutting result. A proper parameter setup is also responsible to avoid overheating and prepare a smooth cutting action.
Follow the thermal precautions given at the top of the article and you are all good to go.
Post-processing is also a significant task to finally achieve a proper production. Follow the safety considerations available for laser cutting polycarbonate.
Laser cutting polycarbonate VS acrylic
Polycarbonate and acrylic are two different materials. In terms of applying similar cutting methods, both can result in contrasting. Let’s take a look at the similarities and dissimilarities of laser cutting polycarbonate and acrylic.
Laser Cutting Polycarbonate | Laser Cutting Acrylic |
---|---|
Polycarbonate is a thermoplastic polymer known for its strength, durability, and impact resistance. It is transparent and commonly used as a substitute for glass due to its lightweight and shatterproof properties. | Acrylic, also known as PMMA (polymethyl methacrylate) or Plexiglas, is a transparent thermoplastic that resembles glass but is lighter and more impact-resistant. It is often used as a cheaper alternative to glass in various applications. |
Polycarbonate absorbs fiber laser wavelengths, making it suitable for cutting with fiber lasers. However, care must be taken to avoid excessive heat buildup and potential thermal damage to the material. | Acrylic is transparent to CO2 laser wavelengths, making it well-suited for cutting with CO2 lasers. CO2 lasers are commonly used for cutting acrylic due to their ability to produce clean, precise cuts with minimal heat-affected zones. |
When laser cutting polycarbonate, it's essential to control heat buildup to prevent melting or charring of the material. Fiber lasers are typically used for cutting polycarbonate, and proper parameter optimization is crucial to achieve clean, precise cuts. | Acrylic cuts cleanly and efficiently with CO2 lasers, which are well-suited for cutting through the material without excessive heat buildup. CO2 lasers offer high precision and can produce intricate designs with smooth, polished edges. |
Laser-cutting polycarbonate can sometimes result in rough or melted edges due to heat buildup during the cutting process. Proper parameter optimization and post-processing may be necessary to achieve smooth, clean edges. | CO2 lasers produce clean, polished edges when cutting acrylic, resulting in high-quality finished products with minimal post-processing required. Acrylic is well-suited for applications where optical clarity and edge quality are critical. |
Polycarbonate is commonly used in applications requiring impact resistance and durability, such as safety shields, protective covers, and machine guards. Laser-cutting polycarbonate is suitable for creating custom shapes and designs in these applications. | Acrylic is widely used in signage, displays, lighting fixtures, and architectural applications due to its clarity, versatility, and ease of fabrication. Laser-cutting acrylic allows for precise cutting of intricate designs and letters for these applications. |
We can offer customers accessories for CNC router machines and CNC milling machines, including cutting tools (such as mills, drills, bits, and tools), tool holders, ER collets, dust collectors, as well as upgrading components such as rotary tables or automatic tool changers. We also sell accessories for CNC laser machines, such as focus lenses, rotary attachments, risers, automatic feeders, fume extractors, and water chillers. Our selection of accessories for CNC plasma cutters in stock is second to none, with everything from plasma cutting tips, torches, and nozzles to drag shields, electrodes, and air filters. Accessories for CNC wood turning lathe machines are also available for purchase online at STYLECNC, including drive centers, revolving centers, blades, chisels, tool rests, faceplates, and safety equipment such as face shields and dust masks. Additionally, you can find and buy some software for CNC programming and simulation at STYLECNC.
We have free online training. You can come to STYLECNC for training in factory. We can also assign technician for door-to-door training with some charge.
1. User Manual.
We provide document instructions for CNC machine installation, operation and debugging steps with pictures and texts.
2. Staff training.
Prepare training plans and make training handouts. After you purchase STYLECNC CNC machine, we can provide systematic training for users.
3. Telephone support.
After we receive a user's technical support request or fault report, we will immediately contact the user by phone and guide the user to solve the problem.
4. Remote connection service.
After the customer authorizes, the technical support personnel can enter the customer's system through a remote connection to help the customer solve the problem. It can be remotely connected to the customer's system to make programming adjustments on the customer's system, so as to ensure that the system produces the maximum benefit for the user.
5. On-site service.
Under the authorization of the customer, enter the customer's software management system, regularly check the system operation status, and predict the possible problems of the CNC machine in the future; if the engineer needs to understand the judgment and solve the problem on the spot, our company will arrange the engineer as soon as possible at the fastest speed rush to the scene.
6. Regularly visit customers.
After the user purchases the CNC machine, arrange after-sales engineers to visit the customer regularly (online or on-site visits). On the one hand, prevent failures, and on the other hand, respond to various problems in a timely manner. You can also ask the user Some experiences or suggestions during the process can be used as suggestions for CNC machine optimization in the future.
7. Establish a dedicated emergency response team.
To ensure that when emergencies occur, technical personnel can be called quickly, emergency technical plans are formulated immediately, and problems are solved first.
Yes, we offer paid/free ArtCAM, Type3, Mach3, Cabinet Vision, Alphacam, UcanCAM, LaserCut, CypCut, CypOne, RDWorks, EZCAD, Laser GRBL, Inkscape, EzGraver, SolveSpace, LaserWeb, LightBurn, Archicad, and more software with CNC machines purchased from STYLECNC, so it will be more convenient for you to operate the machine.
We helped a lot of beginners in CNC machines, if you have a basic knowledge of computers and are willing to spend a little time on learning, it is not too hard. When you ordered a CNC machine from STYLECNC, we will send the user manual and operating videos to you, you can also get the 24/7 free online service by calling, email, whatsapp, livechat or remote desktop with teamviewer.
The cost of your shipment will depend on its origin, destination, value of CNC machines shipped, service, package weight, size, delivery times, and some unexpected considerations. To get the shipping cost of your CNC machine from STYLECNC, feel free to tell us.
You are welcome to get a free quotation by filling up the form with name, email, detailed address, product and requirements, we'll estimate the final price for your CNC machine.
Please note, customs fees and additional fees may apply for international shipments. Contact your local customs office for more information.
STYLECNC provides free consultation, business solutions, quotations, and sales services for machines and accessories for sale, and provides technical support for transportation, distribution, installation, commissioning, operation, and repair of sold machines, and provides lifetime installation , debugging and maintenance services for software.
Pre-Sales Service
1. Free Sample Cutting Service: For free sample cutting/testing, please send us your CAD file (PLT, AI), we will do cutting in our factory and make video to show you the cutting process and result, or send samples to you to check the cutting quality.
2. Progressing Solution Design: According to customer’s product processing requirement, we can design the unique solution that supports higher manufacturing efficiency and better processing quality for customer.
3. Customized Machine Design: According to customer's application, we may revise our CNC machine according to customer's convenience and high production efficiency.
After-Sales Service and Technical Support
1. As a professional CNC machine manufacturer and supplier, STYLECNC will supply the CNC machine with training video and user's manual in English for installing, operation, maintenance and trouble-shooting, and shall give technical guide by remote, such as TeamViewer, E-mail, Telephone, Mobile, Whatsapp, Skype, 24/7 online chat, and so on, when you meet some problems of installation, operation or adjusting.
2. You can come to our CNC machine factory for training. We will offer professional guidance, direct and effective face-to-face training. Here we have assembled equipment, all sorts of tools and testing facility. Training Time: 3~5 days.
3. Our engineer will do a door-to-door instruction training service at your local site. We need your help to deal with the visa formality, prepaid traveling expenses and accommodation to us during the business trip and service period before their dispatch.
STYLECNC values your business and always attempts to provide you the best service and support.
No limited warranty is provided by STYLECNC unless your CNC machine was purchased from STYLECNC or an authorized distributor as well as an authorized reseller. Please see below for the warranty information.
As a top CNC machine brand & manufacturer in the world, STYLECNC promise:
1. 1-3 years for the whole CNC machine.
2. Long life-time maintenance, after-sale department will offer 24/7 English online support.
3. Except the damage artificially, we are responsible for offering the fittings free of charge during warranty.
4. After the warranty period expired, you only need to pay the actual maintenance cost.
5. Certificate support: CE, FDA, SGS.
Note: If you can't find your answer in the FAQs above, please ask a new question in the form below.
Ask Your Question
Asking questions is essential in CNC machining for fostering understanding and encouraging exploration, allowing individuals to gain deeper insights and challenge assumptions, ultimately facilitating learning and innovation.