I REALLY love this CNC foam router. It makes my foam work much easier. Fully automatic, high precision. I am not an expert but this kit works well for my purpose. Highly recommended.
3 Axis Foam CNC Router Machine for Styrofoam, EPS & XPS
Foam CNC router machine comes with a 3 axis for foam board cutting and foam relief carving, and a 4 axis swing head for 3D foam mold making, as well as a 4th axis for rotary milling and cutting Styrofoam, EPS and XPS foam.
- Brand - STYLECNC
- Model - STM1325F
- Supplity - 360 Units in Stock Available for Sale Every Month
- Standard - Meeting CE Standards in Terms of Quality & Safety
- Warranty - One-Year Limited Warranty for Entire Machine (Extended Warranties Available for Major Parts)
- 30-Day Money Back Guarantee for Your Purchase
- Global Logistics and International Shipping for You
- Free Lifetime Technical Support for End-Users & Dealers
- Online (PayPal, Trade Assurance) / Offline (T/T, Debit & Credit Cards)
A foam CNC router is a professional CNC foam milling machine to cut and mill styrofoam (foam). It is a light CNC machine tool compared with heavy CNC metal cutting and milling machine tools, the rigidity and precision requirements of styrofoam CNC router machines are slightly lower. The CNC foam router machine is produced according to the idea of metal cutting and milling machine tools. The important processing parts of the milling machine are subjected to annealing and other heat treatment processes. After the processing is completed, a three-coordinate measurement is performed to ensure the accuracy of the parts.
Styrofoam is a material formed by high-temperature foaming of polystyrene (PS) and a foaming agent, usually called "foam". When thermoforming, depending on the foaming ratio, it can be made into containers such as disposable tableware, fresh trays, instant noodle bowls, and hamburger boxes. It can also be used as a shock-proof packaging cushion, which is light in weight, strong, but not environmentally friendly, and is gradually turning to paper packaging.
3 Axis Foam CNC Router Machine Features
1. The Z axis can be heightened to 1000mm, which widens the working region to fit the large three-dimensional curved surface processing.
2. A big steel square tube structure by seamless welding and hardening treatment, guarantees it to be strong, reliable, and durable, with a large bearing capacity and long service life.
3. The foam CNC router is equipped with self-lubricating blocks, a four-row ball bearing, and a widened rail, so it can get equal force in all directions to guarantee mechanical precision and strength.
4. Many optional configurations and OEM services are available. According to your requirement, different configurations of CNC foam routers will be offered.
5. High-precision ball screw and Taiwan Hiwin linear square rails, which move smoothly to ensure the machining precision.
3 Axis Foam CNC Router Machine Technical Parameters
Model | STM1325F |
Working area | 1300*2500*600mm |
Table size | 1300*2500mm |
Travelling speed | 12000mm/min |
Working speed : | 10000mm/min |
Spindle power | 6KW |
Spindle speed | 0-18000rpm/min |
Transmission | X/Y rack and pinion, Z ball screw |
Driving motor | Stepper motor(servo motor for choose) |
Control System | DSP (Nc studio for choose) |
Voltage | AC380V/50HZ |
Running Environment | Temperature: 0 degree~45 degree |
Software | Artcam/Type3, other CAD/CAM |
Weight | 2300 KG |
3 Axis CNC Foam Router Machine Details
3 Axis CNC Foam Router Machine Applications
Applicable Materials
CNC foam router is used to shape and cut all types of foams, EPS, polystyrene, polyurethane, styrofoam, polyfoam, wood, composite board, Alucobond, PVC, plastic, acrylic, organic glass, aluminum, copper, and other materials.
Applied Industries
Die and mold industries: Milling and cutting various large foam molds for automobiles, ships, aviation, trains and precision machinery, creating wood molds, food molds (such as cake molds) and other molds for precision manufacturing.
Musical instrument industry: Large 3D curved surface milling and contour cutting.
3 Axis Foam CNC Router Machine for Styrofoam, EPS and XPS Foam Projects
4th Axis CNC Foam Router Machine for Styrofoam, EPS and XPS Foam
4 Axis CNC Foam Router Machine for Styrofoam, EPS and XPS Foam
4 Axis Foam CNC Router Machine Details
Based on the foam model required for solid casting, CNC machining has the obvious advantages of uniform and accurate margins and a good overall appearance of the mold. The important processing parts of the machine tool are subjected to annealing and other heat treatment processes. After processing, the three-axis measurement is performed to ensure the accuracy of the parts. Full-program processing of foam will be the direction of future development.
Benefits of Using a CNC Router for Foam Cutting
The cutting and shaping of foam is changing thanks to CNC routers. With their accuracy, speed, and adaptability, they are perfect for a wide range of uses. Here are a few main advantages of foam cutting with a CNC router.
• Precision and Accuracy: CNC routers cut foam with high precision. They follow exact dimensions and shapes defined in the software. This accuracy reduces material waste and ensures the final product meets specifications.
• Versatility: CNC routers can work with various types of foam, including Styrofoam, EPS, and XPS. This versatility makes them suitable for many projects, from prototypes to artistic designs.
• Speed: Manual cutting techniques can be sluggish and labor-intensive. CNC routers can cut enormous amounts of foam quickly. This speed enables firms to fulfill tight deadlines while increasing productivity.
• Repeatability: Once a design is programmed, the CNC router can replicate it multiple times with consistent quality. This repeatability is crucial for production runs and ensures uniformity in parts.
• Complex Shapes: CNC routers can create intricate designs that may be difficult to achieve manually. This capability opens up new possibilities for creativity and design.
Overall, using a CNC router for foam cutting improves efficiency and quality. It helps businesses stay competitive in a fast-paced market. Whether for prototyping or large-scale production, CNC routers are a valuable asset.
Is a 3 Axis Foam CNC Router Worth the Investment?
Purchasing a 3-axis foam CNC router can be a big choice for both enthusiasts and companies. Knowing the advantages and disadvantages can help you decide if the investment is smart.
The initial cost a 3-axis foam CNC router can be really high. Factors such as machine quality, features, and brand influence the price. However, consider this an investment in efficiency and quality. CNC routers save time and labor costs. They automate cutting processes that would otherwise require manual labor. This efficiency can lead to faster project completion and the ability to take on more work.
The precision of CNC routers minimizes material waste. You can maximize the use of foam sheets, leading to lower material costs over time. This advantage is especially significant in foam cutting, where excess material can add up. With faster production times and reduced waste, businesses can increase their profitability. The ability to take on more projects or offer complex designs can attract more clients and grow revenue.
A CNC router that is properly maintained can last for many years. The time savings, the decrease in errors, and the potential for service expansion can all contribute to a significant return on investment.
Maintenance Tips for 3 Axis CNC Routers Used for Foam Cutting
A 3-axis CNC router needs to be properly maintained in order to function well, particularly when cutting foam. Frequent maintenance increases the machine's lifespan and guarantees efficient operation. Here are some crucial maintenance guidelines to stick to.
• Regular Cleaning: There is a lot of dust and debris produced during foam cutting. Develop the practice of regularly cleaning the workspace. To clear the machine of any remaining foam and debris, use a vacuum or a soft brush. This keeps the environment clean and stops accumulation.
• Lubricate Moving Parts: The moving parts, like rails and lead screws, need proper lubrication to function well. Check these areas regularly and apply a suitable lubricant as recommended by the manufacturer. This ensures everything moves smoothly and reduces wear.
• Router Bit Inspection: The router bit is vital for achieving precise cuts. Examine it regularly for signs of dullness or damage. If the bit is worn out, replace it immediately to maintain cutting quality and efficiency.
• Electrical Check: Regularly look over electrical connections for any wear or loose wires. Secure and intact connections are crucial for the machine’s safe operation and performance.
• Calibration: It’s important to calibrate your CNC router periodically. This process ensures that the machine operates accurately and cuts are precise. Regular calibration can enhance overall performance.
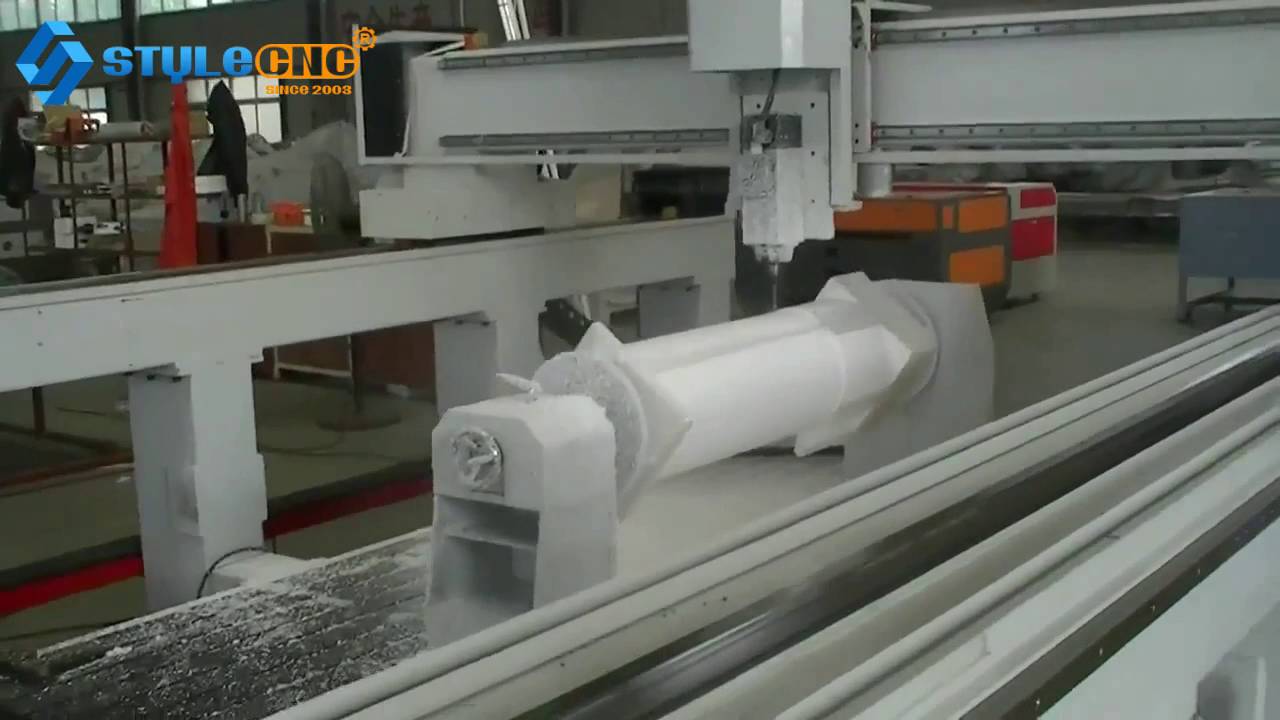